
Managing hazardous material spills is crucial for maintaining workplace safety and protecting the environment. A drum spill pallet plays a vital role in containing leaks and spills, preventing dangerous substances from spreading. Without proper spill containment, hazardous spills can contaminate soil and water, harm workers, and lead to costly fines for non-compliance with regulations like those set by the EPA.
Using a drum spill pallet minimizes risks like chemical exposure, slip-and-fall accidents, and environmental damage. It ensures worker safety while keeping your workplace compliant with safety standards. This guide will help you choose the right spill containment pallet to meet your needs and keep your operations safe.
Key Takeaways
Drum spill pallets help catch dangerous spills and keep areas safe.
Pick a spill pallet that fits your needs, like one for one drum or many drums.
Check and clean your spill pallets often to keep them working well and following safety rules.
Think about the material when choosing a pallet; plastic works for most chemicals, but steel is safer for flammable liquids.
Buying good spill pallets can save money later by avoiding fines and lowering cleanup costs.
What Are Drum Spill Pallets and Why Are They Important?
Definition and Purpose
Drum spill pallets are essential tools for managing leaks, spills, and drips from hazardous materials. These pallets act as a secondary containment system, capturing any spilled liquids before they can cause harm. They typically feature raised edges and built-in sumps designed to hold significant volumes of liquid. Whether you’re handling chemicals, oils, or other hazardous substances, spill pallets help you maintain a safer and more compliant workspace. Most are made from durable materials like high-density polyethylene or steel, ensuring they can withstand tough industrial environments.
By using drum spill pallets, you can prevent environmental contamination, protect your employees, and meet safety regulations. For example, a single drum spill pallet is perfect for storing one drum, while larger models can accommodate multiple drums. These pallets are a must-have for industries that prioritize spill containment and workplace safety.
Common Workplace Applications
You’ll find spill pallets in a variety of industries. Here are some of the most common uses:
Chemical Manufacturing and Processing: They contain spills from drums holding chemicals, reducing the risk of dangerous leaks.
Automotive and Mechanical Workshops: Perfect for managing oils, lubricants, and fuels, they help prevent slip hazards and environmental damage.
Pharmaceutical and Laboratory Facilities: They safely store hazardous reagents and solvents, protecting both personnel and the environment.
No matter your industry, drum containment pallets play a critical role in keeping your operations safe and efficient.
Benefits of Using Drum Spill Pallets
The benefits of using drum spill pallets go beyond just spill containment. First, they enhance safety by containing spills at the source, reducing the risk of accidents and injuries. Second, they help you comply with environmental regulations, avoiding hefty fines. Third, they save you money by minimizing cleanup costs and preventing legal issues. Additionally, spill containment pallets allow you to store multiple drums safely, maximizing your workspace. Their versatility makes them suitable for everything from large industrial facilities to smaller workshops.
By investing in a reliable spill containment pallet, you’re not just protecting your workplace—you’re also safeguarding the environment and ensuring compliance with safety standards.
Types of Drum Spill Pallets

When it comes to managing spills, choosing the right type of spill pallet is essential. Each type is designed to meet specific needs, whether you’re handling a single drum or managing a larger operation. Let’s explore the most common types of spill containment pallets and how they can work for you.
Single-Drum Spill Pallets
Single-drum spill pallets are perfect for smaller operations or when you need to isolate a single drum. These pallets are compact and easy to move, making them ideal for tight spaces. They typically feature a built-in sump to catch leaks and spills, ensuring your workspace stays clean and safe.
Most single-drum pallets are made from high-density polyethylene (HDPE), which is lightweight and resistant to chemicals. This makes them a great choice for oils and non-corrosive substances. If you’re dealing with aggressive fluids, fluorinated options are available to handle those as well. With their small footprint and reliable containment, single-drum spill pallets are a practical solution for many industries.
Multi-Drum Spill Pallets
If you’re managing multiple drums, multi-drum spill pallets are the way to go. These pallets can hold two, four, or even more drums, depending on your needs. They’re designed to maximize space while providing effective spill containment.
Multi-drum pallets often come with removable non-skid decking grates, making cleanup quick and easy. Some models are forkliftable, allowing you to move them effortlessly. For flammable materials, heavy-duty steel platforms offer the durability and safety you need. Whether you’re in a warehouse or a workshop, multi-drum spill pallets help you stay organized and compliant.
Type | Description |
---|---|
Single drum spill pallet | Designed to hold a single drum. |
Two-drum spill pallet | Can accommodate two drums side by side. |
Four-drum spill pallet | Can hold up to four drums in a compact configuration. |
Modular Spill Pallets
Modular spill pallets give you the flexibility to create a custom containment system. These pallets can be connected to form larger platforms, making them ideal for operations with changing needs. You can start small and expand as your requirements grow.
Modular designs often include high and low-profile options, so you can choose what works best for your space. Many also feature ramp-friendly designs, making it easier to load and unload drums. With their adaptability, modular spill pallets are a smart investment for businesses that need scalable solutions.
Tip: Modular spill pallets are especially useful if you’re working in a dynamic environment where drum storage needs frequently change.
By understanding the different types of spill containment pallets, you can select the one that best fits your operation. Whether you need a single-drum spill tray or a multi-drum platform, there’s a solution out there for you.
Portable Spill Pallets
Portable spill pallets are a game-changer when it comes to flexibility and convenience. These pallets are designed for easy transport, making them perfect for temporary setups or situations where you need to move drums frequently. Whether you’re working in a warehouse, a construction site, or a remote location, portable spill pallets help you stay prepared for unexpected spills.
Most portable models come with features like built-in wheels or forklift pockets, so you can move them without breaking a sweat. Some even have collapsible designs, which makes storage a breeze when they’re not in use. Despite their lightweight construction, these pallets are tough enough to handle heavy loads and resist damage from chemicals or UV exposure.
Portable spill pallets are ideal for industries that require mobility. For example, if you’re managing oil drums at multiple job sites, these pallets let you transport them safely while containing any leaks. They’re also great for emergency response teams that need quick and reliable spill containment solutions on the go.
Pro Tip: Look for portable spill pallets with low-profile designs. They make loading and unloading drums much easier, saving you time and effort.
Specialty Spill Pallets
Spill Pallets for Flammable Liquids
When handling flammable liquids, safety should be your top priority. Spill pallets designed for these materials are typically made from steel, which can withstand high temperatures and reduce fire risks. They often include grounding lugs to prevent static buildup, adding an extra layer of protection.
Spill Pallets for Corrosive Substances
Corrosive substances require pallets made from materials like polyethylene. This material resists chemical reactions, ensuring the pallet stays intact even when exposed to aggressive liquids. These pallets are perfect for industries like chemical manufacturing or laboratories.
Spill Pallets for Oil-Based Materials
Oil-based materials can be tricky to manage, but specialized spill pallets make it easier. These pallets often feature high sump capacities to handle large spills. They’re a must-have for automotive workshops, factories, or any operation dealing with oils and lubricants.
By choosing the right type of spill containment pallets, you can ensure safety and compliance while keeping your workspace organized.
Key Factors to Consider When Choosing a Drum Spill Pallet
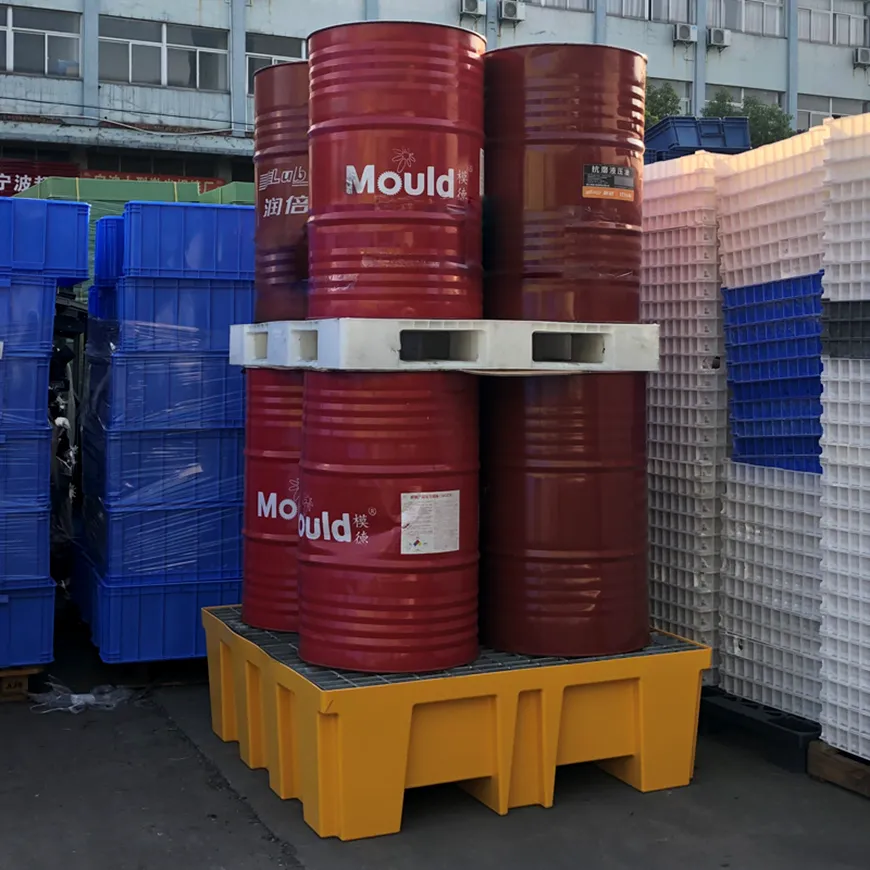
Material Compatibility
Polyethylene vs. Steel Pallets
Choosing the right material for your spill pallets is crucial. Polyethylene pallets are a popular choice because they resist corrosion and work well with many chemicals. They’re lightweight, durable, and ideal for handling hazardous materials like acids, bases, and solvents. On the other hand, steel pallets are perfect for heavy-duty applications. They offer excellent strength and can withstand high impacts, making them suitable for flammable liquids or extreme temperatures.
Criteria | Steel Spill Pallets | |
---|---|---|
Chemical Resistance | Great for acids, bases, and solvents. | Handles corrosive substances effectively. |
Strength and Durability | Lightweight but less impact-resistant. | Strong and impact-resistant. |
UV Exposure | May degrade over time without protection. | Requires coatings for UV resistance. |
Resistance to Corrosion and UV Damage
Not all drum containment pallets are created equal. If you’re storing aggressive chemicals, ensure the pallet material resists corrosion. Polyethylene works well for most chemicals, but steel may be better for extreme conditions. UV resistance is another factor to consider, especially for outdoor use. Prolonged exposure to sunlight can weaken some materials, so look for UV-stabilized options.
Tip: Always match the pallet material to the type of chemicals you’re storing to avoid degradation or chemical reactions.
Capacity and Load-Bearing Requirements
Sump Capacity Guidelines (e.g., 110% of drum volume)
A spill containment pallet must have enough sump capacity to handle potential spills. Regulations often require the pallet to hold at least 110% of the largest drum’s volume. For example, if you’re storing a 55-gallon drum, the pallet should have a minimum capacity of 60.5 gallons. This ensures your spill containment system can manage leaks effectively.
Requirement | Description |
---|---|
Sump Capacity | Must hold 110% of the largest drum’s volume. |
Example | For a 55-gallon drum, the pallet needs 60.5 gallons. |
Weight Limits for Fully Loaded Drums
Weight capacity is just as important as sump capacity. A fully loaded drum can weigh hundreds of pounds, so your pallet must support this weight without buckling. Always check the manufacturer’s specifications to ensure the pallet meets your load-bearing needs.
Space and Storage Constraints
Compact Designs for Tight Spaces
If you’re working in a small area, compact spill pallets are a lifesaver. They maximize your workspace without compromising safety. These designs are perfect for workshops or storage rooms where every square foot counts.
Note: Compact pallets help you stay organized while maintaining a safe and compliant workspace.
Modular Options for Custom Configurations
Modular spill containment pallets offer unmatched flexibility. You can connect multiple pallets to create a custom spill containment system tailored to your needs. This is especially useful for dynamic environments where storage requirements change frequently. Features like ramps and stackable designs make these pallets even more versatile.
Feature | Description |
---|---|
Modular Configurations | Connect pallets to create larger containment areas. |
Additional Features | Options like ramps enhance usability and efficiency. |
Pro Tip: Modular designs are ideal for growing operations. Start small and expand as your needs evolve.
Mobility and Accessibility
Forklift Pockets and Casters
When you need to move spill pallets around your workspace, forklift pockets and casters make life much easier. Forklift pockets allow you to lift and transport pallets safely using a forklift. This feature is especially useful in warehouses or large facilities where drums need to be relocated frequently. You won’t have to worry about spills during transport because the pallets stay stable and secure.
Casters, on the other hand, are perfect for smaller spaces or temporary setups. They let you roll the pallets to different locations without needing heavy equipment. This mobility is a game-changer if you’re working in a dynamic environment. For example, if you’re managing oil drums at multiple job sites, casters make it simple to move them while keeping spills contained.
Tip: Look for spill pallets with locking casters. They keep the pallet in place when stationary, adding an extra layer of safety.
Low Side Walls for Easy Access
Low side walls make loading and unloading drums a breeze. You can easily place drums onto the pallet without lifting them too high, which reduces the risk of accidents. This feature is especially helpful if you’re handling heavy or bulky drums. Some spill pallets even come with ramps, making the process even smoother. Whether you’re using a forklift or doing it manually, low side walls save time and effort.
Cost and Budget Considerations
Balancing Durability and Affordability
Finding the right balance between durability and affordability is key when choosing spill pallets. Polyethylene pallets are often more budget-friendly and work well for most chemicals. Steel pallets, while more expensive, offer unmatched strength and durability. Think about your specific needs. If you’re handling corrosive substances, investing in a high-quality polyethylene pallet might save you money in the long run. For flammable liquids, steel pallets are worth the extra cost.
Note: Don’t compromise on quality just to save a few dollars. A durable pallet will last longer and perform better, giving you more value for your money.
Long-Term Cost Savings from Compliance
Spill pallets help you stay compliant with regulations like EPA standards. Non-compliance can lead to hefty fines, cleanup costs, and even legal issues. By investing in the right pallets, you avoid these risks and save money over time. Plus, a compliant workplace is a safer workplace, which means fewer accidents and lower insurance costs.
Pro Tip: Always check the sump capacity of your spill pallets to ensure they meet regulatory requirements. This small step can save you big headaches later.
Ensuring Regulatory Compliance and Safety Standards
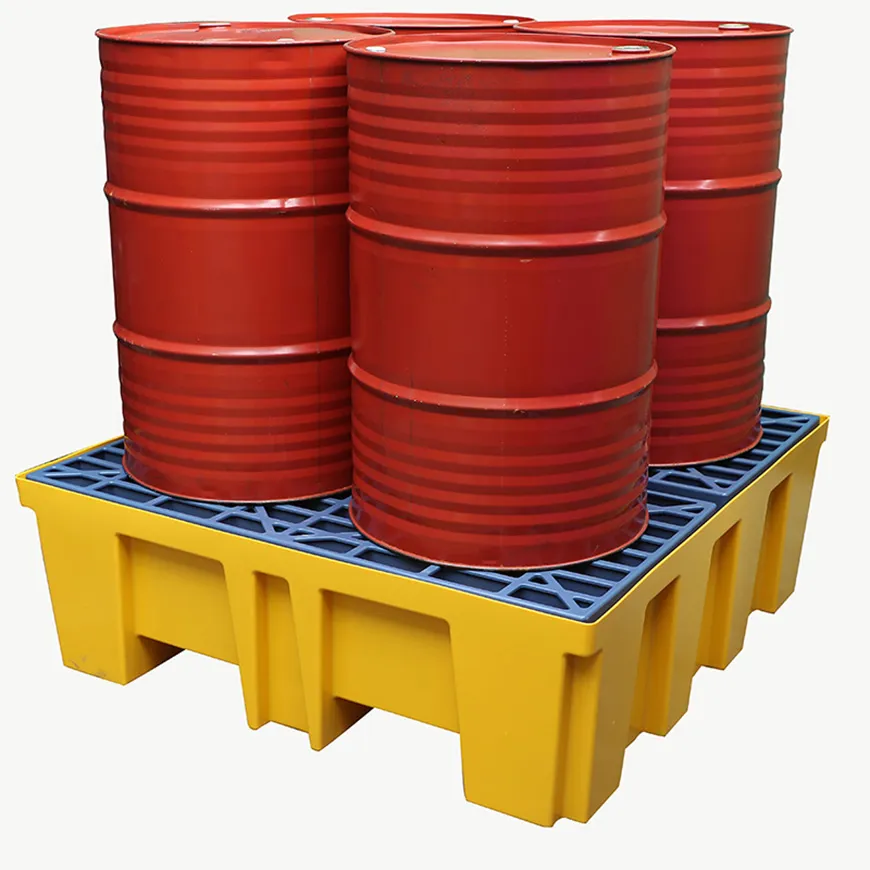
Understanding and adhering to compliance and safety regulations is essential when using spill pallets. These rules not only protect the environment but also ensure the safety of your workplace. Let’s break down the key regulations and requirements you need to know.
Overview of Relevant Regulations
EPA Standards
The Environmental Protection Agency (EPA) enforces strict rules for spill containment. For example, the Resource Conservation and Recovery Act (RCRA) requires secondary containment systems to hold either 10% of the total volume of all containers or the full capacity of the largest container. Additionally, the National Pollutant Discharge Elimination System (NPDES) mandates measures to prevent pollutants from entering U.S. waters. This includes creating a Stormwater Pollution Prevention Plan (SWPPP).
Regulation | Description |
---|---|
EPA (RCRA) | Requires secondary containment for hazardous wastes, ensuring systems can hold 10% of total volume or the largest container’s volume. |
NPDES | Prevents pollutants from entering U.S. waters by requiring proper containment and a SWPPP. |
OSHA Requirements
The Occupational Safety and Health Administration (OSHA) focuses on workplace safety. OSHA requires spill containment pallets to meet specific safety standards, ensuring they can handle hazardous materials without risking employee health.
SPCC Guidelines
The Spill Prevention, Control, and Countermeasure (SPCC) guidelines apply to facilities storing large quantities of oil. These rules require spill pallets to have adequate sump capacity and proper placement to prevent oil spills from reaching navigable waters.
Spill Containment Requirements
Minimum Sump Capacity Standards
To meet regulatory compliance, spill containment pallets must have sufficient sump capacity. Most regulations require the pallet to hold 110% of the largest container’s volume or at least 25% of the total volume of all containers.
Criteria | Requirement |
---|---|
110% of largest container | Must contain 110% of the largest container’s volume. |
25% of total volume | Must hold at least 25% of the total volume of containers. |
Industry-Specific Compliance Needs
Different industries have unique compliance considerations. For example:
Chemical Manufacturing: Spill pallets must handle aggressive chemicals safely.
Automotive Workshops: Containment systems should manage oils and fuels effectively.
Pharmaceutical Facilities: Pallets must prevent hazardous substances from contaminating the environment.
Importance of Documentation and Training
Maintaining Compliance Records
Keeping detailed records of inspections, maintenance, and training is crucial. These documents prove your compliance with safety and regulatory compliance standards. They also help you track the condition of your spill containment pallets and ensure they remain effective.
Employee Training on Spill Management
Proper training prepares your team to handle spills efficiently. Hands-on drills using non-hazardous liquids can build confidence and improve response times. Assign roles during these drills to mimic real-life scenarios. Regular training ensures everyone knows how to use spill containment pallets correctly and safely.
Tip: Conduct timed drills to identify areas for improvement and boost your team’s readiness.
By following these guidelines, you can maintain a safe workplace, protect the environment, and avoid costly penalties.
Practical Tips for Maintenance and Care
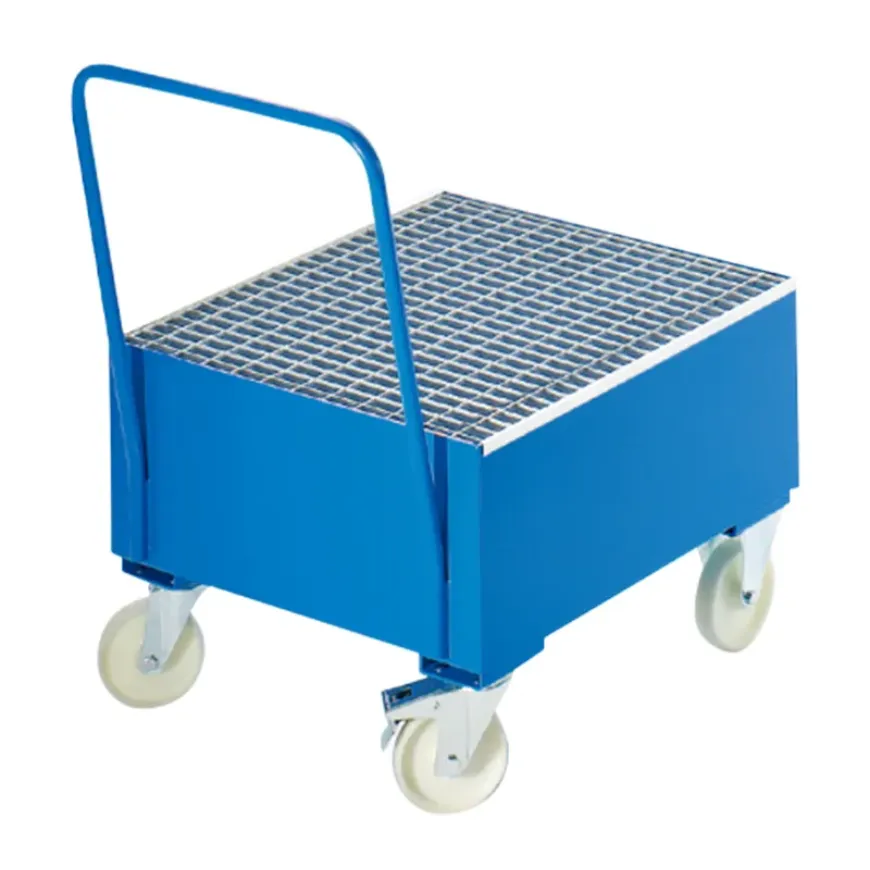
Proper maintenance of your spill pallets ensures they remain effective and compliant. Here’s how you can keep them in top condition.
Regular Inspection and Cleaning
Identifying Signs of Wear and Tear
You should inspect your spill containment pallet at least once a month or after any significant spill. Look for cracks, leaks, or signs of damage that could compromise its integrity. Pay attention to the sump area and edges, as these are common spots for wear. Regular checks help you catch issues early and avoid costly replacements.
Cleaning Procedures for Different Materials
Cleaning your spill pallets is straightforward. Use water and a mild detergent for routine cleaning. If the pallet has been exposed to hazardous chemicals, follow the manufacturer’s guidelines for safe cleaning. Always wear protective gear when handling chemical residues. Keeping your pallets clean not only extends their lifespan but also ensures they’re ready for the next use.
Tip: Schedule inspections and cleanings on the same day each month to build a consistent maintenance routine.
Proper Storage and Handling
Avoiding Overloading
Overloading your spill pallets can lead to structural damage and spills. Always check the weight capacity of your pallet before loading it. For example, a fully loaded 55-gallon drum can weigh over 400 pounds, so ensure your pallet can handle the load. Refer to the table below for regulatory guidelines:
Regulation | Description |
---|---|
EPA (RCRA) | Requires secondary containment for hazardous wastes, mandating systems to hold either 10% of the total volume of containers or the largest container’s volume. |
NPDES | Mandates proper containment measures to prevent pollutants from entering U.S. waters, including the development of a Stormwater Pollution Prevention Plan (SWPPP). |
Safe Placement to Prevent Accidents
Position your spill pallets in accessible locations to allow quick responses to spills. Avoid placing them in high-traffic areas where they could become a tripping hazard. Ensure the ground is level to prevent tipping. Educate your team on proper placement and handling to minimize risks.
Pro Tip: Train employees on spill response protocols to enhance workplace safety and compliance.
Repair or Replacement Guidelines
When to Repair vs. Replace
Not all damage requires a replacement. Minor cracks or surface wear can often be repaired using manufacturer-approved kits. However, if the sump area is compromised or the pallet can no longer hold spills effectively, it’s time for a replacement. Regular inspections help you decide when to repair and when to invest in a new unit.
Sourcing Replacement Parts or Units
When replacing parts or entire spill containment pallets, choose reliable suppliers. Companies like DENIOS, EcoSpill, and American Surplus offer high-quality options. Look for pallets made from durable materials like polyethylene or steel to ensure long-term performance. Investing in quality products saves you money on frequent replacements.
Note: Always match the replacement pallet to the type of chemicals or substances you’re storing to maintain compatibility and safety.
Choosing the right spill pallets is essential for workplace safety, environmental protection, and regulatory compliance. The wrong choice can lead to environmental contamination, workplace hazards, and costly fines. To avoid these risks, evaluate your specific needs carefully. Think about the chemicals you store, the required capacity, and the available space. Use safety data sheets to match the pallet material with the substances you handle. For example, polyethylene works well with many chemicals, while specialized materials are better for strong acids or solvents.
Don’t forget to check local compliance and safety regulations. A spill containment pallet that meets EPA and OSHA standards ensures you stay compliant while protecting your team and the environment. Ready to make a decision? Explore UPQUARK’s drum spill pallet options or consult a supplier for expert advice.
FAQ
What is the purpose of a drum spill pallet?
A drum spill pallet helps you contain leaks and spills from drums holding hazardous materials. It prevents environmental contamination, protects workers, and ensures compliance with safety regulations. Think of it as your first line of defense against workplace spills.
How do I choose the right drum spill pallet for my needs?
Start by considering the type of liquids you store, the number of drums, and your space constraints. Check the pallet’s sump capacity and material compatibility. If you need mobility, look for options with casters or forklift pockets.
Can I use a drum spill pallet outdoors?
Yes, but make sure it’s UV-resistant and durable enough for outdoor conditions. Polyethylene pallets work well for most chemicals, while steel pallets handle extreme temperatures. Always check the manufacturer’s specifications for outdoor use.
How often should I inspect my drum spill pallet?
Inspect your pallet monthly or after any significant spill. Look for cracks, leaks, or signs of wear. Regular inspections help you catch issues early and keep your spill containment system effective.
Are drum spill pallets required by law?
Yes, regulations like EPA standards and SPCC guidelines often require spill containment systems. These rules ensure you prevent hazardous spills from harming the environment or violating safety standards. Always check local regulations to stay compliant.
See Also
Evaluating UPQUARK Marine Absorbents for Oil Spill Management
Selecting Ideal Universal Absorbent Socks for Your Business Needs