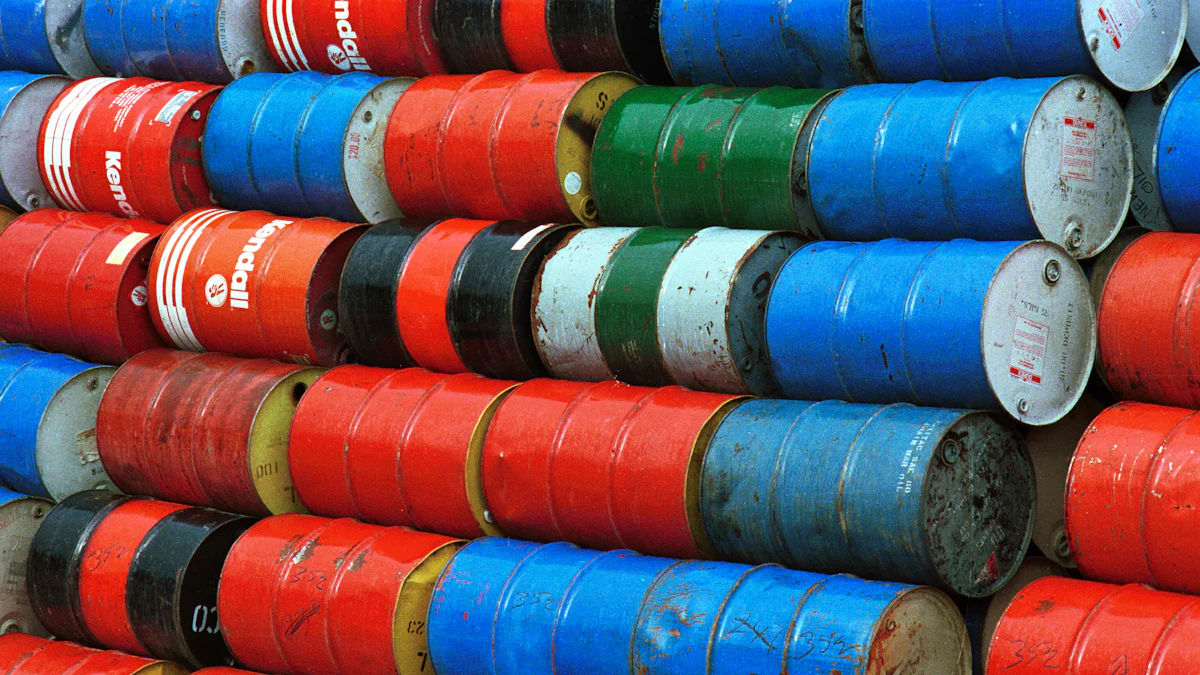
Choosing the right portable secondary containment system isn’t just about convenience—it’s about protecting your operations and your wallet. The wrong choice can lead to unplanned expenses, like costly chemical spill cleanups that range from $5,000 to $10,000. Add in the price of replacing lost chemicals, and the numbers climb even higher. A well-suited system ensures safety, prevents environmental damage, and keeps you compliant with regulations. Whether you’re dealing with hazardous liquids or managing portable spill containment, the right solution saves you time, money, and headaches in the long run.
Key Takeaways
Know the type of liquid you use. Learning about its properties helps pick the right system and avoid problems.
Figure out how much it can hold. Make sure it holds 110% of the biggest container to stop spills and penalties.
Look at your space and location. Pick a system that fits indoors or outdoors and is easy to move if needed.
Check if materials match. Choose a system made of materials that won’t react with your chemicals for safety and strength.
Learn the rules. Understand EPA and OSHA laws to make sure your system is legal and keeps your work safe.
Assessing Your Needs
Identifying the Type of Liquid or Material
Before choosing a portable secondary containment system, you need to know exactly what you’re dealing with. Different liquids and materials have unique properties that require specific containment solutions. Are you handling corrosive chemicals like sulfuric acid or sodium hydroxide? Maybe you’re working with antifreeze agents like propylene glycol or ethylene glycol. Other common substances include citric acid, potassium chloride, and magnesium chloride. Each of these materials reacts differently to containment materials, so understanding what you’re storing or transporting is critical.
Take a moment to review the safety data sheets (SDS) for the liquids you handle. These documents provide essential information about chemical compatibility and potential hazards. By identifying the type of liquid or material upfront, you can avoid costly mistakes and ensure your spill containment system is up to the task.
Determining Capacity Requirements
How much liquid are you planning to contain? This question is key when selecting the right system. A spill containment berm, for example, must have enough capacity to handle the largest potential spill. The Environmental Protection Agency (EPA) often requires secondary containment systems to hold at least 110% of the volume of the largest container.
Think about your worst-case scenario. If a tank or drum leaks, will your system be able to manage the spill? It’s better to overestimate than underestimate. A system with insufficient capacity could lead to environmental damage, fines, or even operational shutdowns.
Evaluating Space and Location Constraints
Where will you set up your containment system? Space and location play a huge role in your decision. If you’re working in a tight area, you’ll need a compact solution that fits without compromising functionality. On the other hand, outdoor setups might require systems that can withstand harsh weather conditions.
Consider the surface where the system will sit. Uneven or rough terrain might call for a more durable and flexible design. Also, think about accessibility. Will you need to move the system frequently? If so, portability becomes a top priority.
By carefully evaluating your space and location constraints, you can choose a system that integrates seamlessly into your operations.
Material and Durability Considerations

Understanding Chemical Compatibility
When choosing a portable secondary containment system, you need to ensure the materials can handle the liquids or chemicals you’re working with. Not all materials are created equal when it comes to chemical resistance. For instance, corrosive substances like sulfuric acid or sodium hydroxide can damage certain containment materials over time. This is why understanding chemical compatibility is so important.
The most common materials used in spill containment products include concrete, polyethylene, and crosslinked polyethylene. Concrete is a traditional option, but it often requires protective coatings to resist chemical damage. Polyethylene is a more affordable choice and works well for many applications. Crosslinked polyethylene, on the other hand, offers enhanced safety with its double-wall design, which helps prevent contamination. By matching the material to the chemicals you handle, you can avoid unnecessary risks and extend the life of your containment system.
Evaluating Durability and Longevity
Durability matters when you’re investing in spill containment solutions. You want a system that can withstand daily wear and tear, as well as exposure to harsh environments. Think about how often you’ll use the system and the conditions it will face. Will it be exposed to extreme temperatures, UV rays, or heavy equipment?
Crosslinked polyethylene systems, for example, are known for their durability and low maintenance needs. They’re built to last, even in tough conditions. Concrete systems, while sturdy, may require frequent repairs or coatings to maintain their integrity. Polyethylene systems are lightweight and easy to handle but might not hold up as well under heavy use.
Comparing Material Options
Here’s a quick breakdown of the pros and cons of different materials:
Concrete Systems: Traditional and sturdy but expensive. They need protective coatings and can collect rainwater, which may mix with chemicals.
Polyethylene Systems: Affordable and easy to store indoors. However, they may expose workers to spills and take up more space.
Crosslinked Polyethylene Systems: Superior protection with a double-wall design. They reduce maintenance but come with higher upfront costs and require regular inspections.
Each material has its strengths and weaknesses. If you need a collapsible containment berm for quick deployment, polyethylene might be your best bet. For long-term use, crosslinked polyethylene offers unmatched safety and durability.
Portability and Setup
Assessing Ease of Deployment
When you’re dealing with spills, every second counts. A portable secondary containment system should be quick and simple to set up. Look for systems that are lightweight and easy to transport. These features make deployment faster and less stressful. Some spill containment products are designed for rapid deployment, allowing you to set them up around machinery or vehicles in just minutes.
Flexibility is another key factor. A good system adapts to different applications, whether you’re containing a small leak or a larger spill. Collapsible containment berms, for example, are perfect for situations where you need to act fast. They fold down for easy storage and pop up when you need them. This makes them a great choice for emergency response teams or industries with unpredictable spill risks.
Evaluating Storage and Transport Features
Storage and transport can make or break your experience with portable spill containment systems. You want a solution that doesn’t take up too much space when not in use. Collapsible spill bunds are a fantastic option here. They fold compactly, making them easy to store in tight spaces.
Transportability is equally important. If you need to move your spill containment berm frequently, choose one with built-in handles or a lightweight design. Some systems even come with carrying cases or wheels for added convenience. These features save you time and effort, especially if you’re working across multiple locations.
Considering Reusability and Maintenance
Reusability is a big plus when it comes to spill containment solutions. A durable system can be cleaned and reused multiple times, saving you money in the long run. Look for materials that resist wear and tear, even after repeated use.
Maintenance is another factor to keep in mind. Some spill containment products require regular inspections or repairs, while others are virtually maintenance-free. Crosslinked polyethylene systems, for instance, are known for their low upkeep needs. By choosing a system that’s easy to maintain, you’ll spend less time worrying about repairs and more time focusing on your operations.
Regulatory Compliance
Understanding EPA and OSHA Standards
Regulatory compliance isn’t just about avoiding fines—it’s about keeping your operations safe and efficient. Agencies like the EPA and OSHA have specific standards for secondary containment systems. These rules ensure you’re prepared for hazardous chemical spills and other emergencies.
Here’s a quick breakdown of key regulations:
Agency | Regulation | Description |
---|---|---|
OSHA | HAZWOPER | Requires containment and spill response measures for hazardous waste cleanup. |
OSHA | General Duty Clause | Mandates addressing workplace hazards, including spills of hazardous materials. |
EPA | RCRA | Sets federal requirements for hazardous waste management, including secondary containment. |
EPA | SPCC | Requires a written plan for preventing spills and managing containment systems for oil storage. |
EPA | Clean Water Act | May require secondary containment for certain facilities to protect water resources. |
Understanding these standards helps you choose a system that meets legal requirements and protects your team and the environment.
Checking for Industry-Specific Requirements
Your industry might have additional rules for spill containment solutions. For example, the EPA’s Spill Prevention, Control, and Countermeasures (SPCC) rule focuses on preventing oil discharges into navigable waters. It applies to facilities handling oil and includes specific guidelines for secondary containment systems.
Key requirements include:
Systems must hold the entire volume of the largest container in case of a leak.
Materials should resist corrosion and be compatible with hazardous substances.
Designs should allow for easy inspection and maintenance.
For industries like oil and gas or chemical manufacturing, these rules are non-negotiable. They ensure your spill containment berm or collapsible containment berm can handle the job effectively.
Looking for Certifications and Testing
Certifications and testing standards are your assurance of quality. A reliable portable secondary containment system should meet these criteria:
The base must be free of cracks and capable of containing leaks or spills.
It should be sloped or designed to allow liquid removal.
It must hold at least 10% of the total container volume or the largest container’s volume.
Secondary containment systems must also prevent liquid migration to soil or water and detect and collect leaks until they’re removed.
By choosing certified spill containment products, you ensure compliance and peace of mind. Look for systems tested for durability and compatibility with hazardous materials. This guarantees they’ll perform when you need them most.
Budget and Maintenance
Balancing Cost and Features
When choosing a portable secondary containment system, balancing cost and features is crucial. You’ll find that prices vary widely depending on the type of system and its features. For example:
SAFE-Tanks can save you up to 90% compared to traditional concrete systems, with no ongoing maintenance costs.
Concrete containment systems often exceed $9,000 for a 1,000-gallon tank, excluding the primary tank’s cost.
Open-top tank systems are cheaper upfront but risk chemical loss during spills, which can lead to disposal costs of $5,000 to $10,000.
If you’re on a tight budget, collapsible spill bunds or portable spill containment products might be a better fit. They’re affordable, easy to deploy, and offer reliable protection. However, don’t sacrifice essential features for a lower price. A system that lacks durability or compatibility with your materials could cost you more in the long run.
Considering Long-Term Value
Think beyond the initial price tag. A temporary containment solution might seem cost-effective now, but how will it hold up over time? Systems like crosslinked polyethylene offer excellent durability and low maintenance, making them a smart investment. SAFE-Tanks, for instance, eliminate ongoing maintenance costs, saving you money over the years.
Also, consider the nature of the liquids you handle. Corrosive substances or environmentally sensitive sites may require more robust systems, which could increase upfront costs. However, these systems often provide better protection and reduce the risk of fines or cleanup expenses.
Exploring Additional Features
Some spill containment products come with extra features that enhance functionality. Portable systems often include spill berms, containment pools, or trays, which are versatile and easy to transport. Quick deployment features minimize spill spread and reduce accidents, making them ideal for emergency situations.
If you frequently move your system, look for collapsible containment berm options. These are lightweight, compact, and simple to store. They’re perfect for industries needing flexibility and portability. By exploring these additional features, you can find a system that meets your needs while offering added convenience.
Choosing the right portable secondary containment system involves balancing your needs, material compatibility, portability, compliance, and budget. Start by evaluating your specific requirements. Experts recommend calculating the containment volume by factoring in dimensions, displacement, and precipitation freeboard. This ensures your system can handle the largest container safely.
A well-chosen system protects your team, the environment, and your bottom line. SAFE-Tanks, for instance, shield workers from splashes and prevent rainwater contamination during leaks.
By consulting experts and prioritizing safety, you’ll find a solution that’s reliable, compliant, and cost-effective. Take the time to make the right choice—it’s worth it.
FAQ
1. What is a portable secondary containment system?
A portable secondary containment system is a temporary solution designed to catch spills or leaks from containers, tanks, or equipment. It’s lightweight, easy to transport, and ideal for industries needing quick spill management.
2. How do I know if my system meets EPA standards?
Check the product specifications for compliance with EPA regulations like SPCC or RCRA. Look for certifications or testing details that confirm the system’s ability to handle hazardous materials safely.
3. Can I reuse a portable containment system?
Yes, most systems are reusable if cleaned and maintained properly. Durable materials like crosslinked polyethylene can withstand repeated use, saving you money over time.
4. What’s the best material for chemical spills?
It depends on the chemicals you handle. Polyethylene works for general use, while crosslinked polyethylene offers better resistance to corrosive substances like acids or alkalis.
5. How do I calculate the capacity I need?
Start with the largest container’s volume. Add 10% for safety, as required by EPA guidelines. Don’t forget to account for displacement and precipitation if the system will be outdoors.
Tip: Always overestimate capacity to avoid compliance issues or environmental risks.
See Also
Selecting Ideal Universal Absorbent Socks for Your Business
Evaluating UPQUARK Marine Absorbents for Effective Oil Spill Response