
Workplace safety isn’t just a box to check—it’s the foundation of a thriving work environment. When you prioritize safety, you’re not only protecting employees but also boosting morale and productivity. Did you know that in 2023, there were 2.6 million reported workplace injury and illness cases, with 946,500 involving days away from work? Here’s a quick breakdown:
Statistic | 2023 |
---|---|
Total injury and illness cases reported | 2.6 million |
Total injuries | 2.4 million |
Cases involving days away from work | 946,500 |
Total fatal work-related injuries | 5,283 |
A safe workplace reduces these numbers, saving lives and cutting costs. For every $1 spent on medical costs, businesses lose $2.30 in productivity. By working together to maintain workplace safety, you create an environment where everyone can thrive.
Key Takeaways
Focus on workplace safety to keep employees safe and happy. A safe place helps workers do better and get hurt less.
Find and fix dangers at work by checking often. Let workers help to make everyone more aware of safety.
Spend money on safety lessons to teach workers. Training often stops accidents and makes workers more responsible.
Follow safety rules by knowing the laws and checking often. Following rules keeps the workplace safe for everyone.
Keep the workspace clean and tidy to avoid accidents. Ask workers to care for their work area.
Identifying and Addressing Workplace Hazards

Creating a safe work environment starts with recognizing potential dangers. By identifying and addressing workplace hazards, you can prevent accidents and protect your team.
Common Types of Workplace Hazards
Workplace hazards come in many forms. Here are some of the most common ones you should watch out for:
Physical Hazards: These include slips, trips, and falls, as well as dangers like excessive noise or extreme temperatures. For example, loud machinery can lead to hearing loss over time.
Chemical Hazards: Harmful substances like gases, solvents, or cleaning agents can cause respiratory issues or skin irritation.
Ergonomic Hazards: Poorly designed workspaces or repetitive motions can lead to musculoskeletal disorders, such as back pain or carpal tunnel syndrome.
Understanding these hazards is the first step toward improving workplace safety.
Conducting Risk Assessments
Risk assessments help you uncover hidden dangers and take action before they cause harm. Follow these steps to conduct an effective assessment:
Identify the Hazards: Walk through your workplace and look for risks. Talk to employees and use safety checklists to ensure nothing is missed.
Decide Who Could Be Harmed: Determine which groups or individuals might be affected and how.
Establish Control Measures: Review existing safety measures and identify areas for improvement.
Record Your Findings: Document the risks and share the information with your team. Provide training on any new safety procedures.
Review Regularly: Update your assessment whenever there are changes in the workplace.
Involving employees in this process is crucial. They know the jobsite best and can point out hazards you might overlook. Plus, when employees feel heard, they’re more likely to support safety initiatives.
Proactive Hazard Mitigation
Once you’ve identified risks, it’s time to take action. Proactive hazard mitigation ensures your workplace stays safe over time. Here’s how you can do it:
Develop and Implement Safety Plans: Create detailed plans to address specific hazards. For example, train employees to handle chemicals safely or set up barriers to prevent falls.
Regularly Update Safety Measures: Workplace conditions change, and so do risks. Continuous monitoring and improvement keep your safety measures effective.
Some companies have excelled in proactive hazard mitigation. For instance, organizations recognized by OSHA’s Voluntary Protection Program have implemented robust safety programs that empower employees to report risks and continuously improve processes. You can follow their lead by fostering a culture of risk awareness and accountability.
By addressing hazards head-on, you create a safer, more productive environment for everyone.
Implementing Safety Training and Education
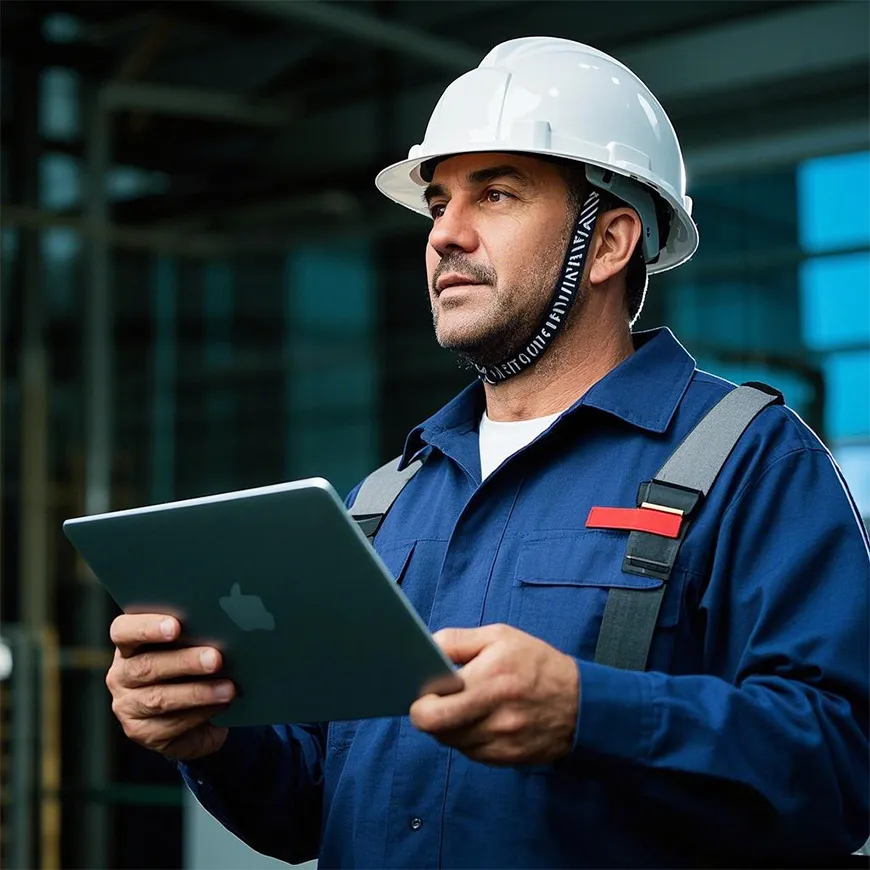
Safety training isn’t just a formality—it’s a game-changer for creating a safer workplace. When you invest in training, you’re not only reducing accidents but also empowering your team to handle risks confidently.
Importance of Safety Training
Raising awareness to reduce accidents
Training helps employees recognize hazards before they become problems. For example, understanding how to handle chemicals or operate machinery safely can prevent injuries. Plus, fewer accidents mean less downtime and lower costs for your business.
Empowering employees with knowledge
When employees know what to do in risky situations, they feel more confident and valued. This sense of empowerment boosts morale and productivity. A well-trained team is also more likely to follow safety protocols, creating a culture of accountability.
Types of Training Programs
Onboarding safety training for new employees
Starting a new job can be overwhelming. Onboarding safety training ensures new hires understand workplace risks and how to avoid them. It’s a great way to set the tone for a safety-first culture from day one.
Periodic refresher courses for all staff
Even seasoned employees need reminders. Regular refresher courses keep safety practices fresh in everyone’s minds. They also allow you to update your team on new regulations or procedures.
Best Practices for Effective Training
Using interactive and hands-on methods
Nobody enjoys boring lectures. Hands-on activities, like fire drills or equipment demonstrations, make training engaging and memorable. Humor and interactive sessions can also help employees retain information better.
Tailoring training to specific roles and risks
Not all jobs have the same hazards. A desk worker doesn’t need the same training as someone handling heavy machinery. By customizing training to fit specific roles, you ensure employees get the knowledge they need most. Start by analyzing job risks and addressing them directly.
Investing in safety training benefits everyone. It reduces workplace disruptions, lowers insurance costs, and improves employee satisfaction. When you prioritize training, you’re building a safer, more productive environment.
Ensuring Compliance with Workplace Safety Standards

Compliance with safety standards isn’t just about avoiding fines—it’s about creating a secure environment where employees can thrive. By understanding regulations, conducting audits, and fostering a culture of accountability, you can ensure your workplace remains safe and compliant.
Understanding OSHA and Industry Regulations
Key OSHA requirements for a safe workplace
The Occupational Safety and Health Administration (OSHA) sets essential guidelines to protect employees. Here are some key requirements:
The General Duty Clause: You must maintain a workplace free from recognized hazards.
Hazard Communication Standard: Provide a written program for hazardous chemicals and train employees on safe handling.
Personal Protective Equipment (PPE) Standards: Ensure employees have and use the right protective gear.
Recordkeeping Requirements: Keep detailed records of work-related injuries and illnesses.
Specific Industry Standards: Follow tailored safety rules for your industry, whether it’s construction, healthcare, or manufacturing.
Understanding these regulations helps you build a foundation for occupational safety and compliance.
Industry-specific compliance standards
Every industry has unique risks. For example, construction sites must address fall protection, while healthcare facilities focus on infection control. Research the standards that apply to your field and ensure your policies align with them.
Conducting Safety Audits
Regular inspections to ensure compliance
Safety audits are your best tool for spotting risks before they become problems. They help you identify unsafe practices, compliance gaps, and potential hazards. Regular inspections also ensure you’re up-to-date with the latest regulations, which is crucial in industries where standards change frequently.
Addressing and documenting violations
When audits uncover issues, act quickly. Fix hazards, update procedures, and document everything. This not only protects your team but also shows regulators that you take workplace safety seriously. Plus, a well-documented process can prevent repeat violations.
Building a Culture of Compliance
Encouraging accountability and safe practices
A strong safety culture starts with leadership. When managers model safe behavior and prioritize ethics, employees follow suit. Make policies easy to understand and encourage open conversations about compliance. Empower your team to call out unsafe practices respectfully.
Recognizing and rewarding safety efforts
Acknowledging safe behavior motivates employees to stay vigilant. Use methods like verbal praise, public recognition, or tangible rewards such as gift cards or extra time off. Celebrate milestones like accident-free days and highlight team achievements. Recognition reinforces the message that safety is everyone’s responsibility.
By focusing on compliance, you create a workplace where safety isn’t just a rule—it’s a shared value.
Maintaining a Clean and Organized Workspace

A clean and organized workspace isn’t just about appearances—it’s a cornerstone of workplace safety and efficiency. When you prioritize tidiness, you’re creating an environment where employees can focus, collaborate, and stay safe.
Benefits of a Tidy Work Environment
Reducing risks of accidents and injuries
Keeping your workspace clean can significantly lower the chances of accidents. For instance:
Cleaning up spills and dust promptly prevents slips, trips, and falls.
Clearing walkways of tools and clutter reduces tripping hazards.
Properly storing materials minimizes injuries from sharp objects or falling items.
A clean work environment also ensures evacuation routes remain clear and reduces fire risks by maintaining proper clearance around electrical equipment.
Enhancing productivity and efficiency
A clutter-free workspace doesn’t just improve safety—it boosts morale and productivity too. Employees feel less stressed in an organized setting. Plus, a clean environment promotes better health by reducing germs, leading to fewer sick days. When your team feels good, they work better.
Tips for Keeping the Workspace Clean
Establishing regular cleaning schedules
Consistency is key to maintaining cleanliness. Here are some practical tips:
Focus on high-traffic and high-touch areas to control germs.
Prohibit food in certain areas to avoid spills and pests.
Stock up on cleaning supplies and PPE to ensure everyone can contribute.
By sticking to a schedule, you’ll keep your workspace safe and welcoming.
Properly storing tools and materials
Proper storage is essential for safety. Always return tools to their designated spots after use. Store flammable materials correctly to prevent fire hazards. Keeping everything in its place not only reduces risks but also saves time when you need to find something.
Managing Clutter and Waste
Implementing waste management systems
Effective waste management benefits both your workplace and the environment. It reduces waste generation, conserves resources, and improves operational efficiency. Plus, it enhances your brand image and boosts employee morale. A sustainable approach to waste can even open up new business opportunities.
Encouraging employees to maintain order
Encourage your team to take ownership of their workspace. Simple habits, like decluttering desks daily or organizing shared areas, go a long way. When everyone pitches in, maintaining order becomes second nature.
By keeping your workspace clean and organized, you’re not just reducing risks—you’re fostering a positive, productive atmosphere where employees can thrive.
Providing Proper Tools and Equipment

Having the right tools and equipment is essential for workplace safety and efficiency. When you invest in quality tools, you’re not just improving performance—you’re protecting your team from unnecessary risks.
Importance of Quality Tools and Equipment
Preventing injuries from faulty equipment
Low-quality or poorly maintained tools can lead to serious accidents. For example:
Dull blades or damaged ladders increase the risk of injuries.
Using the wrong tool for a task can result in cuts, stabs, or even equipment failure.
Poor tool control allows unnoticed damage, which can cause tools to fail during use.
By choosing high-quality tools, you reduce these risks and create a safer work environment. Plus, effective tool control prevents financial losses from missing or damaged equipment.
Enhancing employee performance and safety
When employees have access to reliable tools, they can focus on their tasks without worrying about malfunctions. This boosts productivity and morale. Additionally, tools that fit well and function properly make jobs easier and safer. For instance, using safe lifting techniques with the right equipment minimizes strain and prevents injuries.
Regular Maintenance and Inspections
Checking tools for wear and tear
Routine inspections are key to keeping tools in top condition. Develop a checklist that covers critical components and prioritize equipment based on its importance. For example, regularly inspect power tools for frayed cords or loose parts.
Repairing or replacing damaged equipment
When you spot an issue, act quickly. Repair tools if possible, but replace them if they’re beyond repair. Keeping detailed records of maintenance activities helps you track issues and plan repairs effectively. This not only ensures safety but also demonstrates compliance with workplace regulations.
Training Employees on Equipment Use
Ensuring proper handling of tools
Even the best tools can be dangerous if used incorrectly. Training employees to handle equipment properly reduces accidents and improves efficiency. For example, teaching workers how to operate machinery safely or use PPE correctly can prevent injuries.
Providing manuals and demonstrations
Hands-on demonstrations and clear manuals make training more effective. Interactive sessions, like gamified learning or role-playing, engage employees and help them retain information. Every training program should start with an understanding of workplace risks and include protocols for reporting hazards.
By providing quality tools, maintaining them regularly, and training your team, you’re setting the stage for a safer, more productive workplace.
Encouraging Open Communication and Reporting

Creating a safe workplace starts with open communication. When employees feel heard, they’re more likely to report hazards and suggest improvements. Let’s explore how you can foster transparency, set up effective reporting systems, and respond to concerns the right way.
Fostering a Culture of Transparency
Encouraging employees to voice concerns
Transparency begins with trust. Encourage your team to speak up about safety issues without fear of judgment. Hold regular meetings where employees can share their concerns openly. You can also ask for feedback on current safety practices. When employees see their input leads to real changes, they’ll feel more invested in workplace safety.
Establishing a no-retaliation policy
No one should fear retaliation for reporting a hazard. Make it clear that your workplace has a zero-tolerance policy for retaliation. Put this policy in writing and share it with your team. When employees know they’re protected, they’ll feel safer bringing up potential risks. This creates a culture where safety is everyone’s priority.
Benefits of transparency in workplace safety:
Improves decision-making by providing access to relevant information.
Increases engagement and motivation by valuing employee feedback.
Prevents misunderstandings and reduces conflicts.
Encourages innovation by fostering idea-sharing.
Setting Up Reporting Systems
Anonymous reporting options
Not everyone feels comfortable speaking up in person. That’s where anonymous reporting systems come in. Use secure channels, like encrypted online forms, to protect confidentiality. Employees should also have the option to track their report’s progress and communicate anonymously with safety representatives. This builds trust and ensures concerns are addressed.
Clear procedures for reporting hazards
Make the reporting process simple and straightforward. Provide step-by-step instructions on how to report hazards, whether it’s through a digital platform, a suggestion box, or a hotline. Post these procedures in visible areas, like break rooms or bulletin boards. When reporting is easy, employees are more likely to participate.
Pro Tip: Address reports promptly and transparently. Quick action shows employees that their concerns matter, which strengthens trust in the system.
Responding to Reports Effectively
Investigating and addressing issues promptly
When a report comes in, act fast. Start by documenting the issue and gathering evidence. If someone is injured, prioritize their care by administering first aid or calling emergency services. Then, investigate the root cause of the problem. A thorough investigation prevents similar incidents in the future.
Providing feedback and solutions
Don’t leave employees in the dark after they report a hazard. Share the steps you’ve taken to address the issue. Whether it’s fixing faulty equipment or updating safety protocols, let your team know how their input made a difference. This feedback loop keeps employees engaged and reinforces the importance of reporting.
Best Practices for Responding to Reports:
Take care of affected employees immediately.
Investigate thoroughly and document findings.
Communicate openly with all involved parties.
Update safety plans based on investigation results.
By fostering transparency, setting up effective reporting systems, and responding thoughtfully, you create a workplace where safety concerns are addressed head-on. This not only reduces risks but also builds a stronger, more engaged team.
Maintaining workplace safety isn’t a one-time task—it’s an ongoing commitment. To create a safer environment, you should:
Regularly review and update safety procedures to keep them relevant.
Provide engaging and up-to-date safety training for your team.
Foster a culture where everyone takes responsibility for safety.
Make safety a priority in every operation.
Benefit | Explanation |
---|---|
Enhanced reputation | Attracts top talent and improves employee retention. |
Increased trust and confidence | Builds credibility with stakeholders. |
Financial stability | Reduces risks and ensures steady financial performance. |
Improved productivity | Minimizes disruptions, leading to smoother workflows. |
Cost savings | Lowers expenses related to workplace injuries. |
Reduced absenteeism | Creates a healthier environment with fewer sick days. |
By working together, you can build a safer, healthier, and more productive workplace for everyone.
FAQ
What is the first step to improving workplace safety?
Start by identifying hazards in your workplace. Walk around, observe, and talk to employees about potential risks. Use checklists to ensure you don’t miss anything. Once you know the dangers, you can take action to address them.
How often should safety training be conducted?
You should provide safety training during onboarding and offer refresher courses regularly. Aim for at least once a year or whenever new equipment, procedures, or regulations are introduced. Keeping training fresh helps employees stay prepared.
Why is reporting hazards important?
Reporting hazards helps prevent accidents before they happen. When employees share concerns, you can fix issues quickly. It also shows your team that their safety matters, building trust and encouraging a proactive safety culture.
What tools can help maintain workplace safety?
Use tools like safety checklists, reporting systems, and training programs. High-quality equipment and proper storage solutions also play a big role. Regular maintenance ensures everything stays in good condition, reducing risks.
How can I encourage employees to follow safety rules?
Lead by example. Recognize and reward safe behavior. Make safety policies clear and easy to follow. Create a culture where employees feel comfortable speaking up about concerns. When everyone feels involved, they’re more likely to stay committed.
Pro Tip: Celebrate milestones like accident-free days to keep safety top of mind! 🎉
See Also
Selecting Ideal Universal Absorbent Socks for Your Work Environment
Useful Guidance for Users of Oil Only Absorbent Socks
Understanding Practical Uses of Oil Absorbent Socks
Evaluating UPQUARK Marine Absorbents for Effective Oil Spill Response