
Workplace safety begins with taking the right precautions, and implementing lockout/tagout (LOTO) procedures is a fundamental part of that commitment. Without these measures, accidents are inevitable, and the statistics are alarming. In Massachusetts alone, fatal workplace injuries have surged by 107% over the past decade, with private employers reporting over 55,000 nonfatal injuries in 2023. This highlights the importance of having a well-defined and effective lockout/tagout procedure in place.
Utilizing a lockout/tagout procedure template in Word simplifies this process significantly. It promotes consistency, minimizes errors, and allows for customization to address the unique requirements of specific equipment. As we approach 2025, innovations such as digital templates and smart technology are further enhancing the efficiency of LOTO procedures. By leveraging tools like a lockout/tagout procedure template in Word, you can safeguard your team and maintain a proactive approach to workplace safety.
Key Takeaways
Lockout/tagout (LOTO) procedures are important for keeping workers safe. They stop accidents by controlling dangerous energy during repairs.
Using a lockout/tagout template in Word saves effort and keeps things organized. Templates let you make proper procedures without starting from nothing.
Change your LOTO procedures to fit each machine. Every machine has different energy risks, so adjust your template to handle them well.
Training and clear communication are very important. Make sure all workers know their jobs in LOTO to stay safe and follow rules.
Check and review your LOTO procedures every year. This updates your rules and finds any safety problems that need fixing.
What is a Lockout/Tagout Procedure?
Definition and Purpose
Lockout/tagout procedures, often called LOTO, are essential for workplace safety. These procedures ensure that hazardous energy is controlled during maintenance or repair activities. According to OSHA, lockout/tagout standards protect employees from unexpected equipment startups or energy releases. They outline steps to safely disable equipment until qualified personnel complete their work.
Lockout involves physically isolating energy sources using locks, while tagout uses warning tags when locks aren’t feasible. Together, they prevent accidents and protect workers from injuries caused by hazardous energy. The primary goal of these procedures is to create a safe environment for employees and ensure equipment remains secure during servicing.
Why are these procedures so important? They protect employees from injuries or fatalities, prevent damage to expensive equipment, and promote proper handling of energy sources. By following a consistent step-by-step process, you can ensure safety and compliance in your workplace.
Key Components of Lockout/Tagout Procedures
A well-designed lockout/tagout procedure includes several critical components. Here’s what you need to include:
Essential Component | Description |
---|---|
Intended Use Statement | Explains the purpose of the procedure and its application. |
Shutdown Methods | Details how to shut down machines and control hazardous energy. |
Lockout Steps | Lists the steps for placing and removing locks, tags, and devices. |
Verification Process | Describes how to confirm that the equipment is properly locked out. |
Additionally, you should identify hazardous energy sources, specify lockout device locations, and outline methods for managing residual energy. Clear communication about lockout activities is also vital to ensure everyone stays informed and safe.
Importance of Compliance with Safety Standards
Compliance with lockout/tagout safety standards isn’t just a legal requirement—it’s a lifesaver. Non-compliance can lead to severe consequences, including hefty fines and tragic accidents. For example, OSHA has significantly increased penalties for violations, with some industries facing millions in fines annually. Beyond financial penalties, failing to follow LOTO procedures can result in serious injuries or fatalities.
By adhering to a robust lockout/tagout program, you protect your employees and your business. Regular training, documented procedures, and annual inspections help maintain compliance and ensure your workplace remains safe. Don’t underestimate the importance of a well-executed LOTO policy—it’s an investment in your team’s safety and your company’s future.
Why Use a Lockout/Tagout Procedure Template Word?
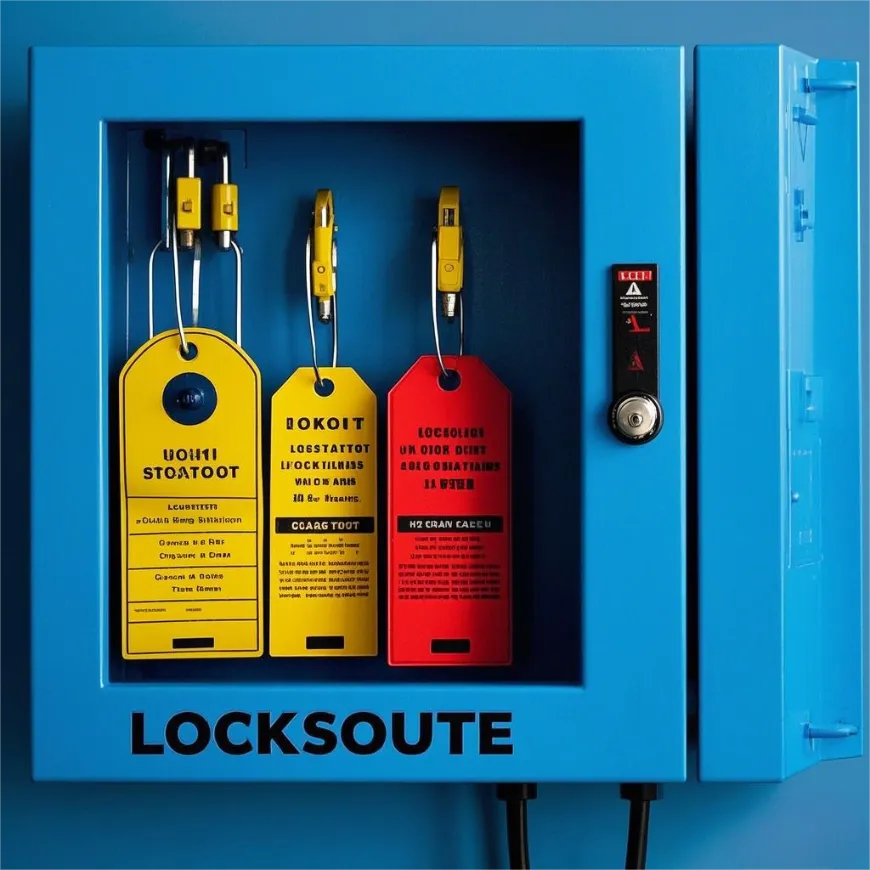
Creating a lockout/tagout procedure from scratch can feel overwhelming. That’s where a lockout/tagout procedure template in Word comes in handy. It simplifies the process, saves time, and ensures your procedures are consistent and compliant with safety standards. Let’s explore why using a template is a smart choice for your workplace.
Benefits of Using a Template
Saves Time and Ensures Consistency
A lockout/tagout procedure template in Word eliminates the need to start from zero. Instead of spending hours drafting procedures, you can use a pre-designed format that includes all the essential components. Templates also ensure consistency across your LOTO policy. By following a structured format, you reduce the risk of missing critical steps, which is crucial for maintaining safety and compliance. For example, tools like Sourcetable offer built-in validation rules that automatically generate accurate and standardized documentation.
Additionally, software solutions can automate parts of the LOTO process. They track lockout statuses, notify team members of updates, and allow you to create procedures in minutes. This time saved can be redirected to other important tasks, like training or equipment maintenance.
Simplifies Customization for Specific Equipment
Every piece of equipment has unique energy control needs. A lockout/tagout procedure template makes it easy to customize steps for specific machinery, whether it’s electrical, hydraulic, or pneumatic. You can tailor the template to include detailed instructions for shutting down, isolating energy, and verifying de-energization. Avoid generic templates for all machines—customization ensures your LOTO policy addresses the unique risks of each device.
Accessibility and Ease of Use
Templates designed for lockout/tagout procedures are incredibly user-friendly. Many include graphical formats, like pictures of lockout steps or maps showing isolation points, making them easier to understand. Digital platforms also enhance accessibility. You can access procedures in real-time, even without Wi-Fi, and share updates instantly with your team. This improves communication and ensures everyone stays on the same page.
Enhancing Compliance with Templates
Using a lockout/tagout procedure template in Word helps you stay compliant with safety regulations. Digital templates log every action taken during the LOTO process, creating a detailed audit trail. This includes who performed the lockout, when it happened, and any issues encountered. These records are invaluable during audits or inspections. Plus, QR codes linked to specific equipment provide instant updates on lockout statuses, reducing human error and improving accountability.
Templates also make it easier to schedule inspections and notify relevant personnel. By keeping everyone informed, you ensure no critical steps are overlooked. This proactive approach strengthens your LOTO policy and keeps your workplace safe.
Step-by-Step Guide to Creating Lockout/Tagout Procedures

Step 1: Define the Purpose and Scope
The first step in creating effective lockout/tagout procedures is defining their purpose and scope. This sets the foundation for your loto policy. Start by clearly stating the intended use of each procedure. For example, explain how the procedures will protect workers during maintenance or servicing. Next, outline the procedural steps for shutdown and isolation of hazardous energy. This ensures everyone knows what to do when handling equipment. Finally, include requirements for testing machines to verify proper lockout.
To make this process even clearer, follow these steps:
Define the range and objective of the lockout/tagout procedure.
Specify who is authorized to perform and oversee the lockout process.
Ensure only trained and competent individuals handle loto procedures.
By addressing these points, you’ll create a strong framework that keeps your team safe and compliant.
Step 2: Identify Roles and Responsibilities
Assigning roles and responsibilities is crucial for a successful loto policy. Everyone involved should know their part. Supervisors play a key role in verifying and maintaining energy control procedures. They also document the issuance of locks and tags. Maintenance associates must understand and apply safety procedures while reporting any violations.
Here’s a breakdown of typical responsibilities:
Supervisors: Ensure proper use of PPE, adherence to procedures, and documentation.
Authorized Workers: Follow established procedures and report issues.
Management: Develop and update lockout policies, supply PPE, and provide funding.
When everyone knows their role, your lockout/tagout procedures will run smoothly and effectively.
Step 3: Outline the Lockout/Tagout Process
Equipment and Energy Source Identification
Before starting any loto procedures, identify all equipment and energy sources. This includes electrical, hydraulic, pneumatic, and other hazardous energy types. Create a detailed list of each energy source and its isolation points. This step ensures no energy source is overlooked, reducing risks during maintenance.
Step-by-Step Shutdown and Isolation Instructions
Once you’ve identified the energy sources, outline the procedural steps for shutdown. Start with preparation for shutdown, ensuring all workers are aware of the process. Then, proceed with equipment shutdown and isolation of energy sources. Apply lockout/tagout devices to secure the equipment. Don’t forget to dissipate any residual or stored energy. Finally, verify isolation to confirm the equipment is in a zero-energy state.
Proper verification of the zero-energy state is critical. It ensures the equipment is safe to work on and prevents unexpected energy releases. By documenting these steps, you create a clear and reliable loto policy template.
Step 4: Verify Energy Isolation
Verifying energy isolation is one of the most critical steps in your lockout/tagout procedures. Before anyone begins working on equipment, you need to confirm that all energy sources have been properly isolated and de-energized. This step ensures the equipment is in a zero-energy state, eliminating the risk of accidental energy release.
How can you verify energy isolation effectively? Start by identifying all energy-isolating devices and ensuring they’ve been operated correctly. Then, use practical methods to confirm de-energization:
Use voltage meters to test for electrical energy.
Inspect pressure gauges for hydraulic or pneumatic energy.
Look for any signs of stored energy, such as movement or residual pressure.
For a thorough check, follow these steps:
Attempt to activate all controls to ensure they’re unresponsive.
Return all controls to the “off” position.
Test for any remaining energy using appropriate tools.
By taking these precautions, you’ll create a safer environment for your team and reduce the chances of accidents during maintenance.
Step 5: Ensure Accessibility and Training
Training Employees on the Procedure
Training is the backbone of any successful loto policy. Without proper training, even the best lockout/tagout procedures can fail. You need to ensure that every employee involved in loto procedures understands their role and the risks associated with hazardous energy.
Start by developing a training program tailored to your organization’s needs. Cover the purpose of lockout/tagout, OSHA standards, and the specific duties of each employee. Include hands-on practice and assessments to reinforce learning. For example, you can conduct simulations where employees apply loto procedures to real equipment.
Don’t stop at initial training. Offer regular refreshers—at least annually or whenever there are changes in job assignments or equipment. Keep detailed records of all training sessions, including dates, trainer names, and attendee signatures. This documentation not only ensures compliance but also helps you track progress.
Inadequate training is a leading cause of loto failures. By investing in comprehensive training, you empower your team to handle hazardous energy safely and confidently.
Storing and Sharing the Document
Accessibility is key to maintaining an effective loto policy template. Your lockout/tagout procedures should be easy to find and understand. Digital formats are a great option. They simplify document control and allow you to update procedures quickly. You can even use graphical representations, like pictures or diagrams, to make the steps clearer.
For added convenience, consider these strategies:
Strategy | Description |
---|---|
Digital Formats | Store procedures electronically for easy access and updates. |
Graphical Representations | Use visuals to enhance understanding of equipment and processes. |
Backup Options | Keep physical binders as backups or mount procedures directly on equipment. |
By combining digital and physical storage methods, you ensure everyone can access the loto policy when needed. This approach keeps your team informed and your workplace safe.
Best Practices for Lockout/Tagout Procedures
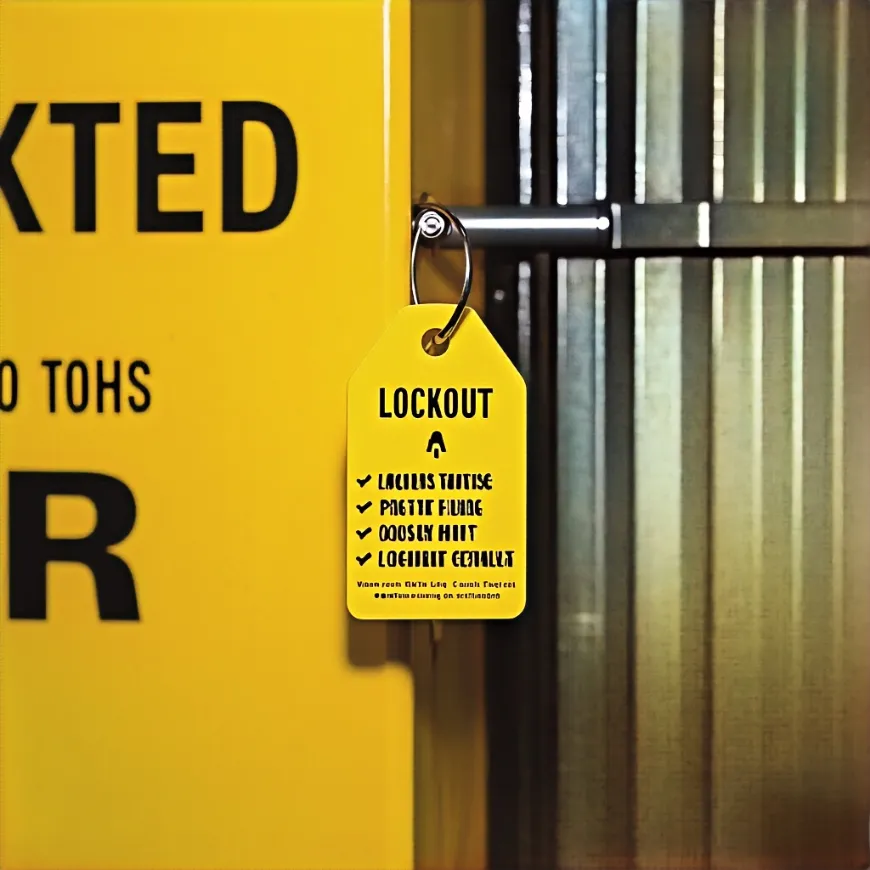
Use Clear and Simple Language
When writing lockout/tagout procedures, clarity is your best friend. Using clear and simple language ensures everyone understands the steps, even under stressful conditions. Workers often perform loto tasks during time-sensitive situations, so avoiding confusion is critical.
Here’s why simplicity matters:
Clear instructions reduce misunderstandings and errors.
Breaking down each step into actionable tasks makes procedures easier to follow.
Straightforward language helps workers stay focused, especially when dealing with hazardous energy.
For example, instead of saying, “Ensure the equipment is de-energized,” you could say, “Turn off the main power switch and test the equipment to confirm it won’t start.” This approach leaves no room for doubt and keeps your team safe.
Regularly Review and Update Procedures
Lockout/tagout procedures aren’t a one-and-done deal. You need to keep them fresh and relevant. OSHA requires annual reviews to ensure procedures remain effective and compliant.
OSHA’s standard states that employers “shall conduct a periodic inspection of the energy control procedure at least annually to ensure that the procedure and the requirements of this standard are being followed.”
Follow these steps to stay on top of updates:
Review all loto procedures annually.
Assign an authorized person (not the regular operator) to inspect each procedure.
Update procedures whenever equipment or processes change.
Regular reviews help you catch outdated steps and maintain the safety of employees. Staying proactive also ensures compliance with regulations.
Provide Comprehensive Training for Employees
Training is the backbone of any successful loto policy. Without it, even the best procedures can fail. Every employee involved in maintenance or repair work must understand how to lockout and tagout equipment properly. Supervisors also need training to oversee the process effectively.
A good training program should:
Cover the basics of loto, including the importance of de-energizing equipment.
Include hands-on practice with locks, tags, and verifying a zero-energy state.
Offer annual refreshers and retraining for changes in job roles or equipment.
Tailor your training to your organization’s needs. Use real-world examples and encourage questions to make the sessions engaging. By investing in thorough training, you empower your team to handle loto procedures confidently and safely.
Conduct Regular Audits for Compliance
Regular audits are essential to keep your lockout/tagout procedures effective and compliant. Without them, your lockout processes can become outdated, leaving your workplace vulnerable to risks. OSHA even mandates annual inspections to ensure your loto policy is up to date and employees are familiar with the steps. So, how do you conduct these audits effectively? Let’s break it down.
Preparation and Planning: Start by defining your audit objectives. Gather all necessary documentation, like your written loto policy and training records. Assemble a team of qualified individuals to carry out the audit.
Reviewing LOTO Procedures and Policies: Take a close look at your written procedures. Are they accurate? Do they reflect the current equipment and processes in your workplace? This step ensures your lockout/tagout procedures stay relevant.
Inspecting LOTO Equipment: Check the condition of your lockout devices. Are they labeled correctly? Are they available when needed? Faulty or missing equipment can compromise safety.
Observing LOTO Procedures in Action: Watch employees as they perform lockout steps. Are they following the loto policy? Interview them to gauge their understanding of the process.
Verifying Employee Training and Competence: Review training records to confirm employees have received proper instruction. Conduct quick tests to ensure they know how to apply the procedures.
Assessing Program Effectiveness: Finally, evaluate the overall effectiveness of your loto policy. Are there gaps in compliance? Identifying deficiencies now can prevent bigger problems later.
Tip: Use a checklist during audits to ensure no step gets overlooked. It’s a simple way to stay organized and thorough.
Skipping audits can lead to unsafe conditions. Lockout/tagout procedures might fail to address new risks, putting your team in danger. Regular reviews reinforce safety practices and help you maintain compliance. By staying proactive, you protect both your employees and your business.
Lockout/tagout procedures are essential for keeping your workplace safe. They protect workers from hazardous energy during equipment maintenance, preventing injuries and accidents. By locking and tagging energy sources, you ensure machines stay off until it’s safe to work on them. Regular training and proper verification of energy isolation are key to making these procedures effective.
Using a lockout/tagout procedure template in Word makes this process easier. It saves time, ensures consistency, and allows you to customize steps for specific equipment. Templates also help you stay compliant with safety standards, reducing risks and improving efficiency.
Now’s the time to act. Use the steps outlined in this guide to create or update your lockout/tagout procedures. A well-designed template can make all the difference in protecting your team and maintaining a safe workplace.
FAQ
What is the purpose of a lockout/tagout procedure?
A lockout/tagout procedure keeps workers safe by preventing accidental energy releases during maintenance. It ensures equipment stays off until it’s safe to work on, reducing the risk of injuries.
Can I use a generic template for all equipment?
No, you shouldn’t. Each piece of equipment has unique energy control needs. Customize templates to include specific instructions for shutting down, isolating, and verifying energy sources for each machine.
How often should I review my lockout/tagout procedures?
You should review them at least once a year. Regular updates ensure your procedures stay effective and compliant with OSHA standards, especially when equipment or processes change.
Do I need to train employees on lockout/tagout procedures?
Yes, training is essential. Employees must understand their roles, the risks of hazardous energy, and how to follow the procedures. Regular refreshers help reinforce knowledge and maintain safety.
Are digital templates better than paper ones?
Digital templates are more accessible and easier to update. They allow real-time sharing and can include visuals like diagrams. However, keeping physical backups ensures availability during technical issues.
See Also
Selecting Ideal Universal Absorbent Socks for Your Work Environment
Useful Tips for Users of Oil Absorbent Socks