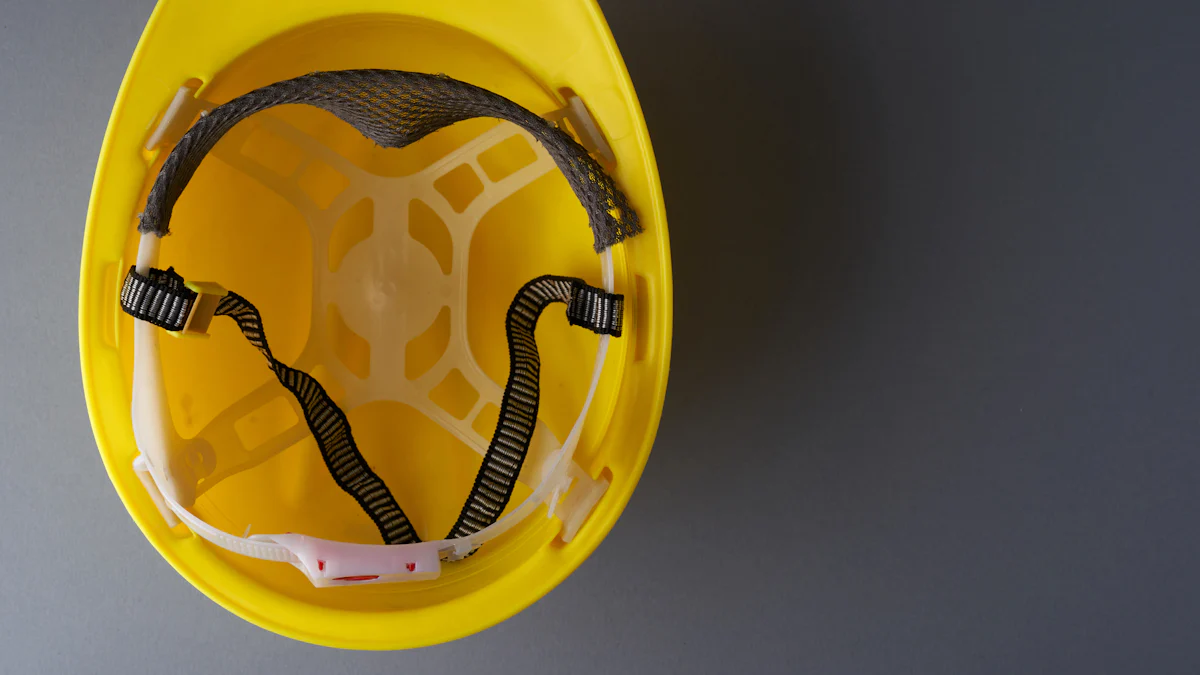
Hard hat in workplace safety signs play a vital role in protecting employees and ensuring compliance with workplace regulations. These signs deliver important safety information, helping workers identify hazards and understand the need for head protection. By choosing the right hard hat in workplace safety signs, you can create a safe work environment and reduce the risk of accidents. Safety signage also supports compliance with OSHA standards, which require clear communication of hazards. Effective PPE safety signs not only enhance employee safety but also foster a culture of personal protection equipment awareness. Selecting the correct hard hat types and strategically placing hard hat in workplace safety signs ensures your workplace meets safety standards while prioritizing worker well-being.
Key Takeaways
Find places in your workplace where hard hats are needed. Check for dangers and make sure safety steps are in place.
Pick safety signs that show risks clearly. Use easy words and familiar pictures so everyone understands.
Choose strong materials for safety signs. Use weatherproof ones like aluminum or coated plastic to last longer.
Put signs at eye level and close to dangers. This helps workers see and understand safety warnings quickly.
Check safety signs often for damage or fading. Replace broken or faded signs right away to keep everyone safe.
Conduct a Risk Assessment for Hard Hat Safety Signs
Identify Workplace Hazards
Determine areas where hard hats are required.
You need to start by identifying areas in your workplace where hard hats are essential. Walk through the site and observe tasks, equipment, and environments that pose risks. Construction sites, oil and gas facilities, and areas with overhead work often require head protection. Use past incident reports and employee feedback to pinpoint locations where falling objects, debris, or equipment impacts are likely. For example, electricians and welders often work in zones where hard hats are mandatory.
A clear understanding of workplace hazards ensures you can implement the right safety measures. The table below highlights common environments and their specific hard hat requirements:
Workplace Environment | Hard Hat Requirement |
---|---|
Construction Sites | Type II head protection with chin straps for falling objects, debris, and equipment impacts. |
Oil and Gas Industry | Type II head protection with integrated eye and face protection for multiple hazards. |
Working from Heights | Head protection with chin straps to prevent helmets from falling off. |
Electrical Work | Non-conductive materials (Class G and Class E) to prevent electrical shocks. |
High and Low-Temperature Environments | Heat-resistant properties (marked “HT”) for high temperatures; preconditioned for low temperatures (marked “LT”). |
High Visibility | High visibility head protection (marked “HV”) for better visibility on jobsites. |
Specialized Work Environments | Headwear that allows for integrated face shields, hearing protection, or communication devices. |
Assess risks such as falling objects or hazardous zones.
Evaluate the specific risks in each area. Falling objects, hazardous zones, and electrical hazards are common threats. For instance, warehouse workers and pipe fitters often face risks from overhead loads. Identify who could be harmed and how, then establish control measures to mitigate these risks. Regularly review and update your assessments to reflect changes in the workplace.
Match Hazards to Appropriate Safety Signs
Select signs that clearly communicate specific risks.
Choose safety signage that conveys important safety information effectively. Use clear wording and symbols to ensure everyone understands the message. For example, mandatory signs like “Wear Hard Hats” inform workers of required actions, while prohibition signs like “No Entry Without PPE” restrict access to unsafe areas.
Use pictograms for universal understanding.
Pictograms enhance the clarity of hazard warning signs, especially in diverse workplaces. A red sign signals immediate danger, yellow indicates caution, and green points to safe areas or equipment. Place these signs close to the hazard and ensure they are visible to all employees. Training workers to recognize and respond to these signs is equally important for maintaining safety.
Understand Hard Hat Safety Standards and Regulations
Research Compliance Requirements
Review OSHA and ANSI Z89.1-2014 guidelines.
Understanding compliance requirements is essential for maintaining workplace safety. OSHA mandates that hard hats meet specific safety standards established by ANSI. The ANSI Z89.1-2014 guidelines outline critical aspects of hard hat design, performance, and testing. These include impact resistance, electrical insulation, and water resistance. For example, Class C hard hats are suitable for general construction, while Class E and Class G provide enhanced electrical insulation.
To comply with these standards, ensure your hard hats resist penetration and absorb shock effectively. Daily inspections are also necessary to identify damage or wear. Hard hats must match the specific hazards in your workplace. For instance, workers exposed to electrical risks should use Class E or Class G hard hats. Testing and certification ensure your head protection meets OSHA standards and provides reliable safety.
Ensure signs meet legal standards for design and wording.
Safety signs must adhere to legal requirements for design and wording. OSHA standards specify that signs should clearly communicate important safety information. Use concise language and universally recognized symbols to ensure clarity. For example, a sign stating “Hard Hats Required Beyond This Point” paired with a pictogram ensures everyone understands the message.
Stay Updated on Regulatory Changes
Regularly review updates to safety protocols.
Safety regulations evolve to address emerging risks. Recent updates include enhanced impact protection for hard hats, reducing the risk of concussions. Modern helmets now feature suspension systems that evenly distribute impact forces. These systems improve safety by keeping helmets secure during accidents. Regularly reviewing updates ensures your workplace complies with the latest hard hat safety standards.
Consult safety professionals for guidance.
Safety professionals can help you navigate complex regulations. They provide insights into new features like integrated face shields and ear protection, which enhance head protection. Consulting experts ensures your workplace remains compliant with OSHA standards while prioritizing employee safety.
Ensure Visibility of Hard Hat in Workplace Safety Signs
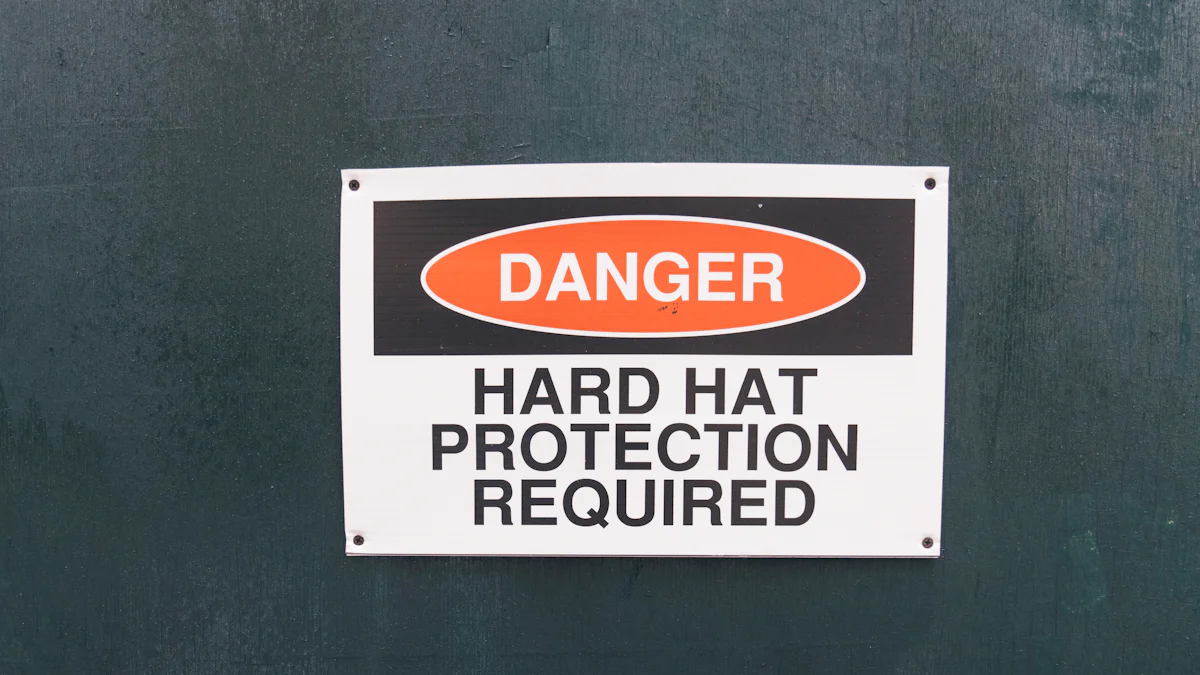
Optimize Size and Design
Use large, bold fonts and high-contrast colors.
To ensure safety signs are effective, you must prioritize their visibility. Use large, bold fonts that are easy to read at a glance. Pair these fonts with high-contrast color combinations to enhance readability. For example, black text on a white background or yellow text on a dark blue background works well. The table below highlights some recommended font and background color pairings:
Font Color | Background Color |
---|---|
Black | White |
Yellow | Dark Blue |
White | Red |
White | Green |
Bright colors like red, yellow, and green are universally recognized for specific hazards. Red signals danger, yellow indicates caution, and green points to safe zones. These colors help workers quickly identify the type of warning or instruction. Proper placement is equally important. Position safety signage at eye level or slightly above to maximize visibility.
Ensure readability from a distance.
Safety signs should be legible from a distance to give workers enough time to react. Place danger, warning, and caution signs at heights between 45 and 66 inches. Emergency equipment signage should be positioned 78 inches above the floor. This ensures workers can spot critical information even in crowded or busy areas. Always test the readability of your signs under real-world conditions to confirm their effectiveness.
Adapt to Lighting Conditions
Use reflective or illuminated signs for low-light areas.
In low-light environments, reflective or illuminated materials improve visibility. Retroreflective materials are particularly effective at night. They reflect light back to its source, making signs visible when illuminated by vehicle headlights or flashlights. High-visibility fluorescent materials work well in daylight by converting UV light into visible light. However, they are less effective at night without a UV source. Choose the material that best suits your workplace lighting conditions to maintain safety.
Test visibility under various conditions.
You should evaluate how well your safety signs perform in different lighting scenarios. Test them during the day, at night, and in dimly lit areas. This ensures workers can see and understand the signs regardless of the time or environment. Regular testing helps you identify and address any visibility issues before they compromise safety.
Choose Durable Materials for Hard Hat Safety Signs
Assess Environmental Factors
Select weather-resistant materials for outdoor use.
Outdoor environments expose safety signs to harsh conditions. You should choose materials that can endure direct sunlight, rain, and wind without deteriorating. For instance, aluminum and stainless steel are excellent options. Aluminum resists rust and corrosion, while stainless steel withstands water, wind, and UV rays. Both materials maintain their structural integrity in extreme weather.
In addition, consider temperature ratings. High-temperature environments, such as boiler rooms, require materials that resist heat without warping. Cold environments demand materials with low-temperature ratings to prevent cracking. Moisture resistance is also critical. Signs in areas with frequent washdowns or constant humidity should use materials like resin or plastic, which repel water effectively.
Opt for materials that withstand wear in high-traffic areas.
High-traffic zones, such as warehouses or construction sites, expose signs to impacts and abrasions. You should select materials that resist chipping, scratching, and industrial impacts. For example, resin and laminated plastic are durable and low-maintenance options. These materials ensure your safety signage remains legible and effective, even in demanding conditions.
Invest in Long-Lasting Options
Use materials like aluminum or laminated plastic.
Durable materials reduce the need for frequent replacements. Aluminum offers a lightweight yet strong solution for both indoor and outdoor use. Laminated plastic provides additional protection against scratches and fading. Both materials are easy to clean, ensuring your hard hat safety signs stay visible and professional-looking over time.
Material | Properties |
---|---|
Aluminum | Lightweight, strong, durable; not susceptible to rust or corrosion; easy to clean and maintain. |
Stainless Steel | Resistant to water, wind, and sunlight; durable for outdoor use. |
Resin | Resistant to various weather elements; low maintenance. |
Plastic | Durable and easy to clean; suitable for outdoor conditions. |
Apply UV-resistant coatings to prevent fading.
UV radiation can cause significant damage to safety signs, leading to fading, cracking, and weakening. You can extend the lifespan of your signs by applying UV-resistant coatings. These coatings form a protective barrier that blocks harmful rays, preserving the color and structural integrity of the signs. This ensures your hard hat safety signage remains clear and effective, even after prolonged exposure to sunlight.
Tip: Regularly inspect your safety signs for damage or fading. Replace any compromised signs immediately to maintain workplace safety and compliance.
Strategically Place Hard Hat Safety Signs
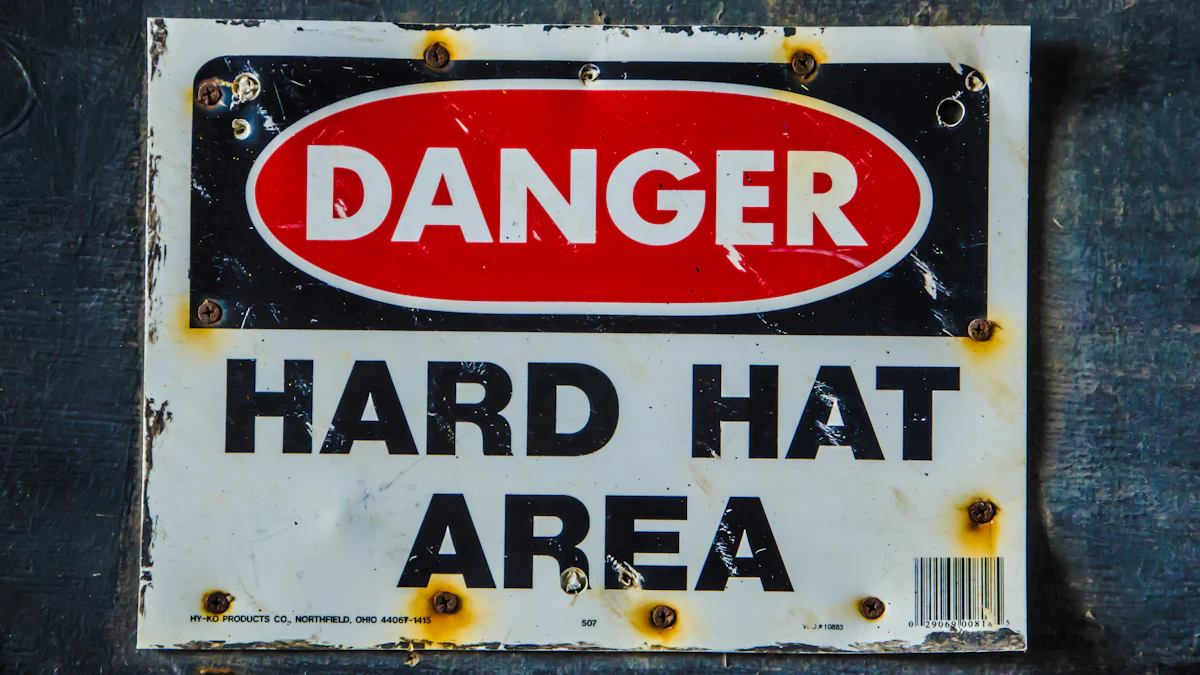
Identify Key Locations
Place signs at entrances to hazardous areas.
You should always position hard hat signs at the entrances of hazardous zones. These areas often have a high risk of falling objects or other dangers that require protective headgear. Posting safety signage at these entry points ensures workers are immediately aware of the need for hard hats before entering. For example, construction sites, warehouses, and industrial facilities benefit from clear signage at access points.
Key locations for these signs include:
High Traffic Zones: Place signs in areas where workers frequently pass, such as corridors, entrances, and exits.
Near Specific Hazards: Position signs close to hazards like electrical panels or areas with overhead work.
Eye-Level Positioning: Mount signs at eye level to ensure they are easily visible and readable.
Position signs at eye level for maximum visibility.
Placing signs at eye level improves their visibility and ensures workers can read them without adjusting their gaze. This placement makes the message clear and easy to understand. For example, danger and caution signs should be at a height where workers can see them while performing tasks.
Danger, Warning, and Caution signs should be positioned at eye level to ensure they are visible to workers while they are engaged in their tasks, highlighting the importance of immediate awareness of hazards.
Avoid Clutter and Obstructions
Space signs appropriately to prevent overcrowding.
You should avoid placing too many signs in one area. Overcrowding can confuse workers and reduce the effectiveness of each sign. Instead, space them out to ensure each message stands out. For example, in a warehouse, position signs at intervals along pathways or near specific hazards.
Remove objects that block the view of signs.
Ensure nothing obstructs the view of your safety signs. Clear away equipment, tools, or other objects that might block visibility. Workers should be able to see the signs from a distance without any hindrance. Regularly inspect the workplace to confirm that all signs remain unobstructed and effective.
Tip: Conduct periodic checks to ensure signs are visible and properly spaced. This practice helps maintain a safe and organized workplace.
Choosing the right hard hat in workplace safety signs is essential for maintaining a safe work environment. These signs provide immediate warnings and instructions, helping workers recognize hazards and use head protection effectively. To ensure safety, prioritize visibility by using bold fonts and high-contrast colors. Select durable materials like aluminum for outdoor signs to withstand harsh conditions. Strategically place signs at eye level and near hazards to maximize their impact. Proper placement and compliance with OSHA guidelines significantly reduce workplace accidents. By investing in effective safety signs, you create a safer and more organized workplace for everyone.
FAQ
What are the key features of effective hard hat safety signs?
Effective signs use bold fonts, high-contrast colors, and clear symbols. They must be durable, weather-resistant, and easy to read from a distance. Proper placement at eye level ensures visibility.
Tip: Use reflective materials for low-light areas to enhance visibility.
How often should you inspect hard hat safety signs?
Inspect signs monthly to check for damage, fading, or obstructions. Replace worn or illegible signs immediately to maintain safety and compliance.
Note: Regular inspections prevent accidents caused by unclear or missing signage.
What materials work best for outdoor safety signs?
Aluminum and stainless steel resist rust, corrosion, and harsh weather. Laminated plastic and resin also work well in outdoor environments.
Material | Best Use Case |
---|---|
Aluminum | General outdoor use |
Stainless Steel | Extreme weather conditions |
Laminated Plastic | High-traffic outdoor areas |
How do you ensure compliance with OSHA standards?
Follow OSHA and ANSI guidelines for sign design, wording, and placement. Use certified materials and regularly update signs to meet regulatory changes.
Reminder: Consult safety professionals to stay informed about new compliance requirements.
Why is proper placement of safety signs important?
Proper placement ensures workers see and understand signs before entering hazardous areas. Eye-level positioning and strategic spacing improve visibility and effectiveness.
Tip: Avoid overcrowding signs to prevent confusion and ensure clarity.
See Also
Selecting Ideal Universal Absorbent Socks for Your Work Environment
Evaluating UPQUARK Marine Absorbents for Effective Oil Spill Response