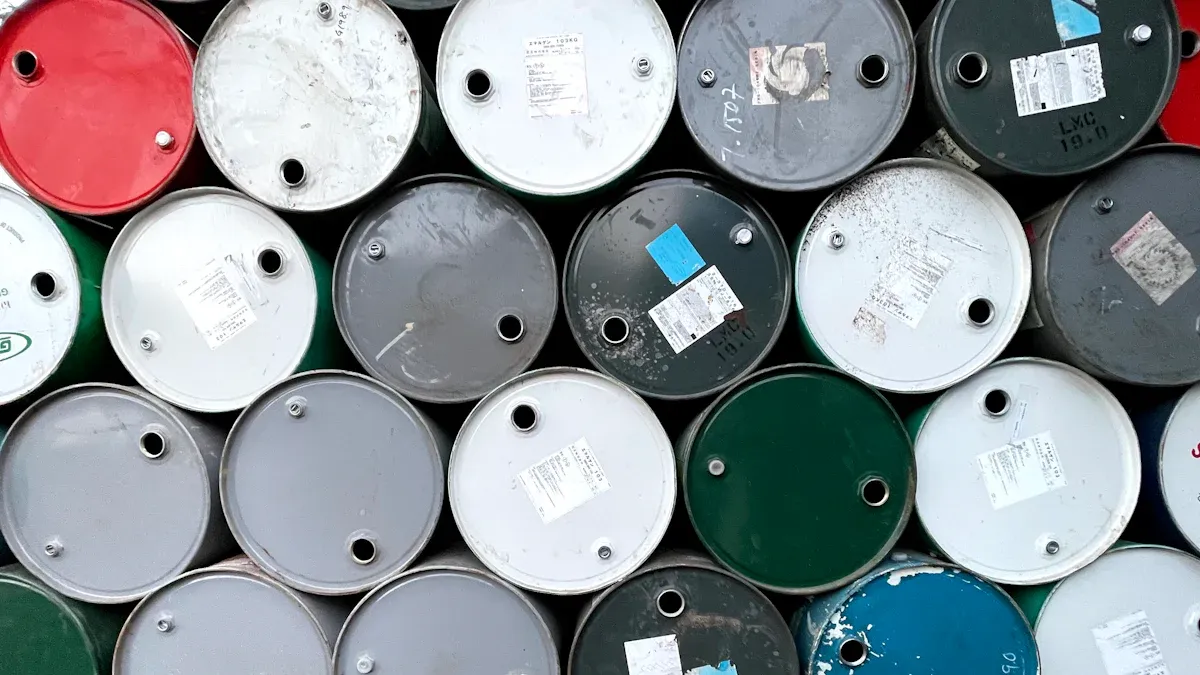
When you think about industrial safety, one tool stands out for its effectiveness: the containment basin. These structures are designed to catch spills, leaks, or drips from storage containers, keeping hazardous substances from spreading. By doing so, they protect workers, the environment, and your operations.
Containment basins play a vital role in preventing contamination of soil and water. For example, chemical plants handle large amounts of dangerous materials daily. They must meet strict EPA and OSHA regulations to avoid environmental damage and ensure safety. Without these basins, the risk of exposure to toxic or flammable chemicals increases significantly.
Chemical plants must take great care to follow EPA and OSHA regulations to minimize the chances of contamination of the environment with, and human exposure to, toxic, corrosive, flammable, or chemically reactive chemical levels.
By using containment basins, industries can comply with regulations, reduce risks, and create safer workplaces.
Key Takeaways
Containment basins stop dangerous spills from spreading to keep areas safe.
They help industries follow important safety and environmental rules like EPA and OSHA.
Industries such as oil, gas, chemicals, and wastewater rely on these basins.
Picking the right basin depends on the materials and industry needs.
Checking and fixing basins often keeps them working and following rules.
What Is a Containment Basin?
Definition and Primary Purpose
A containment basin is a specially designed structure that helps you manage spills, leaks, and drips from industrial operations. Its main job is to act as a safety net when primary containment systems, like tanks or drums, fail. By capturing hazardous substances, it prevents them from escaping into the environment. This makes it an essential tool for industries handling chemicals, oils, or other dangerous materials.
You’ll often find containment basins in places like chemical plants, oil refineries, and wastewater treatment facilities. They’re built to meet strict regulations, such as the EPA’s Spill Prevention, Control, and Countermeasure (SPCC) rule. These rules ensure that facilities have systems in place to protect soil and water from contamination. For example, secondary containment systems must hold at least 10% of the total volume of the primary container or 100% of the largest container, whichever is greater.
Role in Secondary Containment
Secondary containment systems, like containment basins, provide an extra layer of protection. They’re designed to catch spills or leaks that escape from primary containment systems. Think of them as your backup plan. If a tank holding hazardous chemicals starts leaking, the secondary containment system ensures the spill doesn’t spread.
Here’s why secondary containment is so important:
It prevents hazardous substances from polluting soil and water.
It helps you comply with environmental regulations, like OSHA’s chemical storage guidelines.
It reduces the risk of accidents and protects workers.
A table below highlights some common applications of secondary containment systems:
Application Type | Description |
---|---|
Oil and Gas Industry | Prevents fuel spills from contaminating groundwater or the environment. |
Chemical Storage | Used in industries storing chemicals or hazardous waste on-site. |
Wastewater Runoff Basins | Manages runoff and prevents contamination. |
Mining Holding Ponds | Contains materials in mining operations. |
Secondary Containment Systems | Includes bolted or welded steel tanks or concrete vaults for added safety. |
Key Features and Design Considerations
When choosing a containment basin, you need to consider its features and design. The right basin should be durable, resistant to chemicals, and capable of handling the specific materials you work with. For example, some basins use geotextile materials coated with a protective layer to resist tearing and puncturing. Others are made from concrete or steel for added strength.
Design considerations also depend on your industry. For instance, basins in the oil and gas sector must handle hydrocarbons without leaking. Meanwhile, basins for chemical storage need to withstand corrosive substances. Engineers often design these systems to meet specific flow rates, UV resistance, and solidification capacities. A well-designed containment basin ensures you stay compliant with regulations while protecting the environment.
“Adaptable designs and compliance with regulatory standards are key to constructing effective containment basins,” according to engineering research. These systems must also account for factors like soil type and rainfall to prevent runoff contamination.
By understanding these features, you can select a containment basin that meets your needs and keeps your operations safe.
Industrial Uses of Containment Basins
Spill Containment and Prevention
Containment basins are your first line of defense when it comes to spill containment and spill prevention. They’re designed to catch and hold any spill or leak that escapes from primary storage systems. This ensures that hazardous substances don’t spread and cause harm to the environment or your workplace. Whether you’re dealing with oil, chemicals, or other hazardous materials, these basins provide reliable spill protection.
Secondary containment systems, like containment basins, are built to meet strict regulatory standards. For example, they must hold at least 110% of the largest primary container’s volume. This ensures there’s enough capacity to manage spills effectively. By using durable materials that resist leaks, these systems help you maintain safety and compliance.
Storage of Hazardous Materials
If your operations involve chemical storage or other hazardous materials, containment basins are essential. They act as a safety net, capturing leaks or spills before they can cause damage. This is especially important in industries like chemical manufacturing, where even a small spill can lead to serious consequences.
Containment basins also simplify spill management. They keep spills contained in one area, making cleanup faster and easier. Plus, they reduce the risk of accidents by preventing hazardous substances from spreading. With the right containment system in place, you can focus on your operations without worrying about unexpected spills.
Environmental Protection and Compliance
Protecting the environment is a top priority for any industry. Containment basins play a crucial role in this effort. They prevent hazardous substances from contaminating soil and water, reducing the environmental impact of spills. By using secondary containment systems, you can ensure that your operations meet environmental regulations and avoid costly fines.
These basins are more than just a compliance tool. They’re an investment in sustainability. By preventing leaks and spills, they help you minimize waste and protect natural resources. This not only benefits the environment but also enhances your company’s reputation as a responsible operator.
Tip: Regularly inspect your containment basins to ensure they remain effective. This simple step can save you time, money, and headaches in the long run.
Emergency Response and Cleanup
When a spill happens, quick action is critical. Containment basins play a huge role in helping you respond effectively. They keep hazardous materials from spreading, giving you time to manage the situation safely. Whether it’s a small leak or a major spill, these basins act as your first line of defense.
You need a solid plan for spill and leak response. This includes having the right tools and training your team to act fast. Containment basins make this process easier. They hold the spilled material in one place, so you can focus on cleanup without worrying about further contamination. For example, if a chemical containment basin captures a spill, your team can quickly remove the hazardous material without it seeping into the ground.
Here’s how containment basins support emergency response:
Immediate Containment: They stop the spill from spreading, reducing the risk of harm to workers and the environment.
Simplified Cleanup: By keeping the spill localized, they make cleanup faster and more efficient.
Regulatory Compliance: Using containment systems ensures you meet safety and environmental standards during emergencies.
Imagine dealing with a spill without a containment basin. The cleanup would take longer, and the risk of environmental damage would increase. That’s why industries rely on these systems as part of their spill cleanup solutions. They’re not just for prevention; they’re essential for managing emergencies too.
Tip: Regularly inspect your containment basins. This ensures they’re ready to handle spills when you need them most. A well-maintained system can save you time, money, and stress during an emergency.
By integrating containment basins into your spill and leak response plan, you’ll protect your operations and the environment. They’re a smart investment for any industry handling hazardous materials.
Types of Containment Basins

Material-Based Types
Plastic Containment Basins
Plastic containment basins are lightweight and versatile. They’re often made from materials like high-density polyethylene (HDPE) or polyvinyl chloride (PVC). These materials resist tears, punctures, and environmental stress, making them ideal for industries handling chemicals or oil and fuel. HDPE basins, for instance, can last for decades under proper conditions. PVC basins, on the other hand, offer flexibility and perform well in environments with temperature fluctuations.
If you need a cost-effective solution for managing spills, plastic basins are a great choice. They’re easy to install and maintain, which makes them popular in industries like chemical manufacturing and oil storage.
Concrete Containment Basins
Concrete containment basins are built for durability. These permanent installations are perfect for long-term use in facilities that store hazardous materials. They’re commonly used in wastewater treatment plants and chemical plants. Concrete’s strength ensures it can handle heavy loads and resist damage from corrosive chemicals.
However, concrete basins require proper sealing to prevent leaks. Regular inspections help maintain their effectiveness and ensure compliance with environmental regulations.
Steel Containment Basins
Steel containment basins are known for their strength and resistance to extreme conditions. They’re often used in the oil and fuel industry to manage spills and leaks. Steel basins can handle high temperatures and corrosive substances, making them a reliable choice for industrial applications.
These basins are typically coated to prevent rust and extend their lifespan. If you’re looking for a robust solution, steel basins are worth considering.
Design-Based Types
Portable Containment Basins
Portable containment basins offer flexibility. You can easily move them to different locations, making them ideal for temporary spill containment. These basins are often used in emergency response situations or for short-term projects involving oil and fuel.
Their lightweight design allows for quick deployment. Plus, they’re available in various sizes to suit your specific needs.
Fixed Containment Basins
Fixed containment basins are permanent structures designed for long-term use. They’re commonly found in facilities that handle large volumes of chemicals or hazardous materials. These basins provide reliable spill containment and help you comply with environmental regulations.
Fixed basins are often made from durable materials like concrete or steel. They’re built to withstand harsh conditions and provide consistent performance over time.
Industry-Specific Applications
Oil and Gas Industry
In the oil and gas industry, containment basins play a critical role. They’re used for chemical containment, spill prevention, and managing hazardous materials. For example, containment berms help prevent oil and fuel spills from contaminating the environment.
Chemical Manufacturing
Chemical manufacturing facilities rely on containment basins to manage spills and leaks. These basins ensure compliance with EPA and OSHA regulations while protecting workers and the environment.
Wastewater Treatment
In wastewater treatment plants, containment basins are essential for managing runoff and preventing contamination. They’re designed to handle large volumes of water and chemicals, ensuring safe and efficient operations.
Tip: Choose a containment basin that matches your industry’s specific needs. This ensures optimal performance and compliance with regulations.
Benefits of Using Containment Basins
Ensuring Regulatory Compliance
You know how strict regulations can be when handling hazardous materials. Containment basins help you meet these requirements with ease. They’re designed to comply with rules like the EPA’s Spill Prevention, Control, and Countermeasure (SPCC) guidelines. These basins ensure that your facility has the right systems in place to prevent spills from contaminating the environment.
By using a chemical containment basin, you can avoid hefty fines and legal troubles. These systems show regulators that you’re serious about safety and environmental protection. Plus, they make audits less stressful since you’ll already have the necessary safeguards in place.
Tip: Regularly inspect your containment basins to ensure they remain compliant with current regulations. Staying proactive can save you time and money.
Enhancing Environmental Safety
Protecting the environment is more important than ever. Containment basins play a huge role in keeping hazardous materials from polluting soil and water. They act as a barrier, stopping spills before they can cause harm. This not only protects natural resources but also helps you maintain a positive reputation as an environmentally responsible operator.
These basins also reduce the risk of long-term damage. For example, a well-maintained chemical containment basin can prevent leaks from seeping into groundwater. By investing in these systems, you’re contributing to a safer and cleaner environment for everyone.
Note: A small investment in containment systems today can prevent costly environmental damage tomorrow.
Improving Spill Containment Efficiency
When a spill happens, every second counts. Containment basins make managing spills faster and more efficient. They keep hazardous materials in one place, so you can focus on cleanup without worrying about further contamination. This saves you time and reduces the risk of accidents.
The design of these basins ensures they can handle spills of various sizes. Whether it’s a minor leak or a major incident, you’ll have the tools to respond effectively. By improving spill containment efficiency, you’re not just protecting your operations—you’re also safeguarding the environment and your team’s safety.
Reminder: Choose a containment basin that matches your specific needs. The right system can make all the difference in managing spills effectively.
Reducing Costs and Operational Risks
When you think about industrial operations, reducing costs and minimizing risks are always top priorities. Containment basins, like chemical containment basins, help you achieve both. They’re not just about compliance or safety—they’re also a smart financial investment.
Here’s how they save you money. First, containment basins prevent spills from spreading, which means you avoid expensive cleanup efforts. Cleaning up a spill that contaminates soil or water can cost thousands, if not millions, of dollars. With a containment basin in place, you stop the problem before it gets out of hand.
Second, they reduce the risk of accidents. Spills can lead to fires, chemical reactions, or worker injuries. These incidents disrupt operations and rack up costs. By containing hazardous materials, you create a safer work environment and avoid costly downtime.
Did you know? Studies show that disaster risk reduction measures, like containment basins, provide economic returns four times greater than their costs. That’s a huge benefit in terms of avoided losses and operational stability.
Containment basins also make financial sense when you look at the big picture. The initial investment includes construction, maintenance, and risk assessments. However, the long-term savings far outweigh these costs. For example, using a chemical containment basin ensures you’re prepared for emergencies, reducing the likelihood of fines or lawsuits.
By investing in containment systems, you’re not just protecting your operations—you’re also protecting your bottom line. It’s a win-win. So, if you’re looking for a way to cut costs and lower risks, containment basins are the way to go.
Tip: Regular maintenance of your containment basins keeps them effective and ensures you get the most value from your investment.
Containment basins are essential for keeping your operations safe, compliant, and environmentally responsible. They’re used across industries like oil and gas, chemical manufacturing, and wastewater treatment to prevent spills and protect natural resources. Whether it’s managing hazardous materials in mining holding ponds or ensuring compliance with EPA’s SPCC rule, these systems are vital for maintaining safety and minimizing risks.
By investing in containment solutions, you’re not just meeting regulatory standards—you’re actively contributing to environmental protection efforts. These basins help you prevent contamination, reduce cleanup costs, and create a safer workplace. If you’re handling hazardous materials, it’s time to explore how a chemical containment basin can enhance your operations. The benefits are clear: improved safety, better compliance, and a stronger commitment to protecting the environment.
Remember, every spill you prevent is a step toward a safer and more sustainable future.
FAQ
What industries benefit the most from containment basins?
Industries like oil and gas, chemical manufacturing, and wastewater treatment rely heavily on containment basins. These systems help manage hazardous materials, prevent spills, and ensure compliance with environmental regulations. For example, a chemical containment basin is essential for safely storing corrosive substances in chemical plants.
How do I choose the right containment basin for my needs?
Start by considering the materials you handle and your industry’s requirements. For chemicals, a chemical containment basin made from durable, corrosion-resistant materials works best. Also, think about whether you need a portable or fixed design based on your operations.
Tip: Consult with an expert to ensure your choice meets regulatory standards.
Are containment basins reusable?
Yes, many containment basins are reusable, especially those made from durable materials like steel or HDPE. Regular maintenance and inspections keep them effective. However, always clean them thoroughly after a spill to avoid contamination or damage.
Do containment basins require regular maintenance?
Absolutely! Regular inspections ensure your containment basin stays effective. Check for cracks, leaks, or wear and tear. For a chemical containment basin, ensure it’s resistant to the materials you store. Maintenance helps you avoid costly repairs and ensures compliance with safety regulations.
Can containment basins handle extreme weather conditions?
Yes, many containment basins are designed to withstand harsh environments. For example, steel basins resist high temperatures, while HDPE basins handle UV exposure. Always choose a basin suited to your location’s climate and the materials you store.
Reminder: Extreme weather can weaken some materials over time. Regular checks are essential.
See Also
Evaluating UPQUARK Marine Absorbents For Effective Oil Cleanup
Practical Uses and Benefits of Oil Absorbent Socks