
Choosing the right fall protection tie off points is crucial for maintaining workplace safety. Fall protection tie off points act as the backbone of your fall protection system, ensuring that safety lanyards and other equipment perform as intended. Without reliable fall protection tie off points, workers are exposed to greater fall hazards, which can result in serious injuries or even fatalities. For instance, relying on uncertified anchor points or neglecting regular inspections can weaken their reliability. Additionally, excessive slack in the tie-off or improper angles can heighten the risk of accidents. By prioritizing secure and compliant fall protection tie off points, you can minimize these risks and foster a safer work environment for everyone.
Key Takeaways
Use approved tie-off points to stay safe. Unapproved ones can cause accidents.
Check anchor points often for damage or wear. This keeps your safety system working well.
Know the difference between permanent and temporary anchor points. Pick the right one for how long and what the job needs.
Teach workers how to use and check fall protection systems. Trained workers make fewer mistakes that could be unsafe.
Follow OSHA rules. Anchor points must hold at least 5,000 pounds per worker to stay safe.
Understanding Fall Protection Tie-Off Points
What Are Fall Protection Tie-Off Points?
Fall protection tie-off points are secure locations or devices where you can attach fall protection equipment, such as lanyards or harnesses. These points act as the foundation of your fall protection system, ensuring that workers remain safely tethered while working at heights. Tie-off points can be permanent, temporary, or even natural, depending on the job site and the type of work being performed. For example, permanent options include roof anchors or rigid lifelines, while temporary solutions might involve beam clamps or tripods. In rare cases, natural elements like sturdy trees or large rocks may serve as tie-off points. Regardless of the type, these points must meet safety standards to ensure they can handle the forces generated during a fall.
The Role of Anchor Points in Fall Protection
Anchor points play a critical role in keeping workers safe. They prevent severe injuries or fatalities by stopping falls before workers reach the ground. These points also support fall protection systems by providing a secure attachment for harnesses and lanyards. Additionally, anchor points absorb and distribute the forces generated during a fall, protecting both workers and the structure. Industries like construction, roofing, and maintenance rely heavily on anchor points to safeguard employees working at heights. Whether you need a permanent or temporary solution, anchor points offer flexibility to suit different environments and job requirements.
Common Misconceptions About Tie-Off Points
Many workers mistakenly believe that any sturdy-looking structure can serve as a tie-off point. This assumption can lead to dangerous outcomes. Not all structures are designed to handle the forces of a fall, and using uncertified points increases the risk of failure. Another misconception is that once installed, anchor points require no further attention. In reality, regular inspections and maintenance are essential to ensure their reliability. By understanding these misconceptions, you can make informed decisions and prioritize safety on the job site.
Types of Fall Protection Tie-Off Points

Permanent vs. Temporary Anchor Points
When choosing between permanent and temporary anchor points, you need to consider the nature of your work and the duration of the project. Permanent anchors are installed directly into a building’s structure, making them ideal for ongoing maintenance or long-term use. These anchors are durable, reusable, and capable of handling heavy loads. However, they require professional installation, regular maintenance, and come with higher costs.
Temporary anchors, on the other hand, are portable and designed for short-term projects. They are cost-effective, easy to install, and versatile for various applications. Despite these advantages, temporary anchors are less durable and may lack the strength of permanent options. Frequent replacement and the potential for system failure make them less reliable for high-risk tasks.
Tip: Always assess the specific requirements of your job before deciding between permanent and temporary anchor points.
Structural vs. Natural Tie-Off Points
Structural tie-off points are engineered solutions, such as roof anchors, beam clamps, or lifeline systems. These points are designed to meet safety standards and provide reliable support for fall arrest systems. They are commonly used in construction, roofing, and industrial settings.
Natural tie-off points, like sturdy trees or large rocks, may seem convenient but often lack the reliability of structural options. While they can serve as a last resort in certain outdoor environments, you must ensure they meet the required load capacity and safety standards.
Note: Structural tie-off points are generally safer and more predictable than natural ones. Use natural points only when no other options are available.
Pros and Cons of Different Types of Anchor Points
Each type of anchor point has its strengths and weaknesses. Permanent anchors offer long-lasting durability, strong load capacity, and quick connections after installation. However, they are expensive, require professional setup, and need regular inspections.
Temporary anchors are affordable, easy to install, and adaptable to various situations. They are widely available and do not require specialized training for setup. Yet, they lack the strength and durability of permanent options, making them unsuitable for all applications.
Anchor Type | Advantages | Disadvantages |
---|---|---|
Permanent Anchors | Durable, reusable, strong load capacity | Costly, difficult to install, needs maintenance |
Temporary Anchors | Affordable, versatile, easy to install | Less durable, lower strength, frequent replacement |
Understanding the types of fall protection tie-off points helps you make informed decisions and ensures the safety of your team.
Key Considerations for Choosing Tie-Off Points
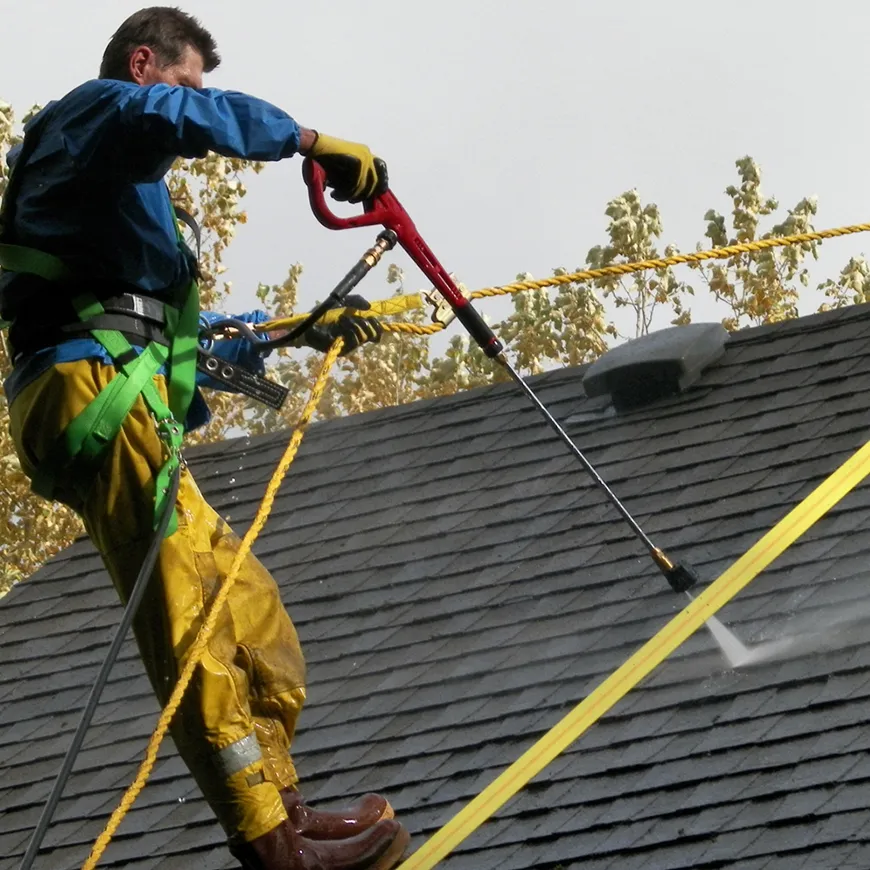
Job-Specific Requirements
Selecting the right tie-off points starts with understanding the specific needs of your job. Each task has unique demands, and your anchorage system must align with them. Consider the following factors:
Purpose: Identify whether the anchorage system will be used for fall protection, fall restraint, or work positioning. Each purpose requires different levels of strength and design.
Compatibility: Ensure the tie-off points are compatible with other components in your fall arrest system. Incompatible materials can lead to disengagement or system failure.
Structure: Verify that the structure supporting the anchorage system can handle the expected impact forces. Weak structures compromise safety.
By addressing these requirements, you can ensure your anchorage system meets the demands of your job and keeps workers safe.
OSHA Compliance and Safety Standards
Meeting OSHA regulations is critical when choosing anchor points. These standards ensure the safety and reliability of your fall protection system. Key requirements for anchor points include:
Each anchor point must support at least 5,000 pounds per worker.
Engineered systems designed by qualified individuals may allow for lower load capacities if they maintain a safety factor of at least two.
Anchor points must be installed according to the manufacturer’s guidelines and inspected regularly by a competent person.
Compliance with OSHA regulations not only protects workers but also helps you avoid penalties and legal issues. Always prioritize adherence to these standards when selecting and maintaining tie-off points.
Structural Integrity and Load Capacity
The structural integrity of your anchorage system is non-negotiable. Anchor points must withstand the forces generated during a fall without failure. Evaluate the load capacity of the structure where the safety lifeline will be attached. For example, a personal fall arrest system requires anchor points capable of supporting significant weight and impact forces.
Regular inspections are essential to ensure the structure remains sound over time. Look for signs of wear, corrosion, or damage that could weaken the anchorage system. By prioritizing structural integrity, you can create a safer work environment and reduce the risk of accidents.
Accessibility and Positioning of Anchor Points
The accessibility and positioning of anchor points play a vital role in ensuring worker safety and the effectiveness of your fall protection system. Proper placement allows workers to easily reach anchor points without putting themselves at risk. When anchor points are difficult to access, workers may skip using them altogether, increasing the likelihood of accidents.
Strategic positioning of anchor points minimizes the risk of falls during tethering. You should place anchor points in locations that are both secure and load-bearing. This ensures they can withstand the forces generated during a fall. Additionally, anchor points should be positioned to reduce the swing fall hazard, which occurs when a worker falls and swings into nearby structures or obstacles.
Tip: Always evaluate the work area to identify the safest and most practical locations for anchor points.
Here are some key considerations for positioning anchor points effectively:
Ensure workers can safely reach anchor points without overextending themselves.
Place anchor points in locations that minimize fall distances and reduce swing hazards.
Verify that the structure supporting the anchor point is strong enough to handle fall forces.
Accessibility also impacts how efficiently workers can use the fall protection system. Anchor points that are too high or too low may require additional equipment, such as ladders or scaffolding, which can introduce new risks. By positioning anchor points at an optimal height, you can improve usability and reduce the time spent setting up safety systems.
Proper accessibility and positioning of anchor points not only enhance safety but also encourage workers to consistently use fall protection systems. This proactive approach helps create a safer work environment for everyone involved.
Best Practices for Using Fall Protection Tie-Off Points
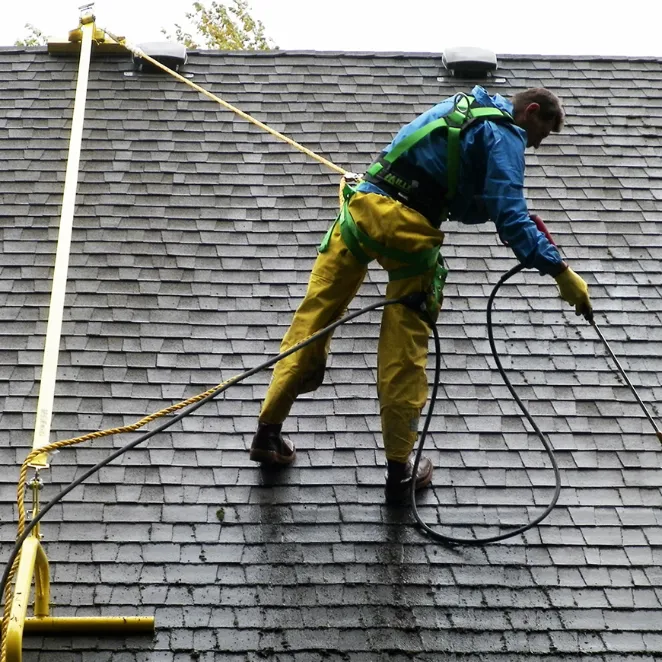
Inspecting Anchor Points Before Use
Inspecting anchor points is a critical step in ensuring the safety of your fall protection system. You should always perform a pre-use inspection before starting work. Begin by checking for visible damage, such as corrosion, cracks, or wear on the anchor materials. Look closely at fasteners to ensure they are tight and free from wear. For temporary anchor points, conduct inspections before each use. Permanent anchor points require routine checks and an annual inspection by a competent person.
Follow these steps to inspect anchor points effectively:
Perform an initial inspection after installation and document the findings.
Check for environmental damage, such as UV exposure or rust.
Verify the integrity of fasteners and ensure they are secure.
Inspect labels for legibility and damage.
Remove any damaged anchor points from service immediately.
Keeping detailed records of inspections is essential for compliance and safety. If you find any issues, replace the anchor point before use. Regular inspections help maintain the reliability of your personal fall arrest system.
Proper Installation and Setup
Proper installation of your fall protection system ensures maximum safety. Start by developing a tailored plan for each job. This plan should address jobsite hazards, equipment requirements, and rescue procedures. Always use equipment that suits the specific hazards of your work environment.
Hire qualified workers to install the system. They should follow the manufacturer’s guidelines and ensure all components are securely attached. Avoid shortcuts during installation, as they can compromise safety. OSHA mandates fall protection equipment for work at heights of six feet or more, so compliance is non-negotiable.
Training workers on proper setup and use of the fall arrest harness is equally important. A well-installed system combined with trained personnel reduces risks and ensures the effectiveness of your fall arrest system.
Avoiding Common Mistakes
Workers often make mistakes that compromise the effectiveness of a fall protection system. One common error is failing to inspect equipment regularly. Always check attachment points, lanyards, and the fall arrest harness for wear or damage. Another mistake is skipping training. Workers must know how to use the system correctly to avoid accidents.
Not using fall protection at all is another critical error. Ensure every worker at height uses a personal fall arrest system. Avoid these mistakes by prioritizing inspections, providing thorough training, and enforcing the use of fall protection systems. These practices create a safer work environment and prevent accidents.
Training Workers on Fall Protection Systems
Training workers on fall protection systems is essential for ensuring their safety while working at heights. Proper training equips your team with the knowledge and skills needed to use fall protection equipment effectively and avoid accidents. A well-designed training program focuses on both theoretical knowledge and practical application.
To create an effective training program, start by performing a hazard assessment. This step helps you identify potential fall hazards and develop procedures to minimize risks. Workers should learn how to recognize these hazards and understand the steps required to mitigate them. Additionally, you must establish clear fall protection and fall recovery procedures to prepare for emergencies.
Your training should also cover the correct use of personal fall protection systems. Workers need to know how to install, inspect, operate, maintain, and disassemble the equipment. This includes understanding proper hook-up, anchoring, and tie-off techniques. For example, when using a fall arrest system, workers must ensure that the anchor points are secure and the equipment is properly adjusted to prevent slack.
Using competent trainers is another critical component. Trainers should have the expertise to teach workers and inspect equipment effectively. Ongoing training is equally important. Regular refreshers help workers stay updated on safety protocols and maintain their confidence in using fall protection systems.
Tip: Always provide hands-on practice during training sessions. This allows workers to familiarize themselves with the equipment and build muscle memory for safe practices.
By investing in comprehensive training, you can reduce the risk of falls and create a safer work environment. Remember, a well-trained team is your first line of defense against workplace accidents.
Maintaining and Inspecting Fall Protection Tie-Off Points

Regular Inspections and Maintenance
Regular inspections and maintenance are essential for ensuring the reliability of your fall protection system. You should inspect anchor points frequently to identify potential issues before they compromise safety. Permanent anchor points require routine checks, while temporary ones need inspection before every use. Always follow the manufacturer’s guidelines for inspection intervals and procedures.
During inspections, look for environmental damage, such as rust, UV exposure, or other signs of wear. Check fasteners to ensure they are secure and free from damage. For permanent systems, schedule annual inspections by a qualified professional to verify compliance with safety standards. Keeping detailed records of these inspections helps you track the condition of your system and ensures compliance with regulations.
Tip: A well-maintained system reduces the risk of failure and extends the lifespan of your fall protection equipment.
Identifying Signs of Wear or Damage
Recognizing signs of wear or damage is critical for maintaining a safe work environment. Corrosion, cracks, and deformation are common indicators that an anchor point may no longer be reliable. Pay close attention to fasteners, as loose or worn components can weaken the entire system.
Environmental factors, such as extreme weather or chemical exposure, can accelerate wear. UV damage, for instance, can degrade materials over time. Always inspect labels and markings for legibility, as faded or damaged labels may indicate prolonged exposure to harsh conditions. If you notice any of these signs, take immediate action to repair or replace the affected components.
Note: Never use an anchor point that shows visible damage or signs of wear. Doing so puts workers at serious risk.
When to Replace or Upgrade Anchor Points
Replacing or upgrading anchor points is necessary when they no longer meet safety standards. You should follow these criteria to determine when replacement is required:
Conduct an initial inspection after installation to confirm safety requirements.
Perform routine inspections for permanent anchor points and pre-use checks for temporary ones.
Look for environmental damage, such as corrosion or UV degradation.
Ensure fasteners are tight and replace any that show wear or damage.
Maintain detailed inspection records for compliance.
Replace any anchor point showing significant wear or damage.
Periodically re-certify anchor points to verify they meet safety standards.
By adhering to these guidelines, you can ensure your fall arrest system remains effective and compliant. Upgrading anchor points may also be necessary when job requirements change or when newer, safer technologies become available.
Reminder: Proactively replacing worn or outdated anchor points prevents accidents and keeps your team safe.
Choosing the right fall protection tie off points is essential for ensuring worker safety and preventing accidents. Proper selection minimizes risks and aligns with OSHA standards, which require anchor points to support at least 5,000 pounds per worker. Regular inspections and maintenance keep these systems reliable by addressing wear, corrosion, or environmental damage.
Prioritizing safety, training, and ongoing maintenance offers long-term benefits. It protects workers, boosts productivity, and reduces costs associated with accidents. A well-maintained fall protection system also enhances your company’s reputation and fosters a culture of safety. By taking these steps, you create a safer and more sustainable work environment.
Reminder: Always inspect anchor points before use and ensure compatibility with your fall protection system.
FAQ
What is the minimum load capacity for a fall protection tie-off point?
OSHA requires each tie-off point to support at least 5,000 pounds per worker. This ensures the anchor can handle the forces generated during a fall. Always verify the load capacity of your anchor points before use.
Can you use any structure as a tie-off point?
No, not all structures qualify as safe tie-off points. Only certified anchor points or structures meeting OSHA standards should be used. Avoid using uncertified or untested points, as they may fail under fall forces.
How often should you inspect fall protection tie-off points?
Inspect temporary tie-off points before every use. Permanent tie-off points require routine checks and an annual inspection by a qualified professional. Regular inspections help identify wear, corrosion, or damage that could compromise safety.
What should you do if a tie-off point shows signs of wear?
Immediately remove the tie-off point from service. Signs of wear, such as corrosion, cracks, or deformation, indicate it may no longer be safe. Replace or repair the anchor point to maintain a reliable fall protection system.
Do workers need training to use fall protection systems?
Yes, training is essential. Workers must learn how to install, inspect, and use fall protection systems correctly. Proper training reduces the risk of accidents and ensures compliance with safety standards. Hands-on practice is highly recommended.
Tip: Regular refresher training helps workers stay updated on safety protocols.
See Also
Selecting Ideal Universal Absorbent Socks for Your Work Environment
Useful Guidance for Users of Oil Only Absorbent Socks
Understanding Practical Uses of Oil Absorbent Socks
Evaluating UPQUARK Marine Absorbents for Effective Oil Spill Response