
Secondary containment berms are raised barriers designed to stop spills from spreading. They act as a safety net, keeping hazardous liquids contained and protecting the environment from contamination. Whether you’re dealing with oil, chemicals, or other dangerous substances, these berms help you stay in control. Plus, they play a big role in meeting regulatory standards. For example, the EPA’s 40 CFR Part 112 outlines specific requirements for spill prevention, while OSHA ensures worker safety during spill response.
Regulatory Body | Regulation/Standard | Description |
---|---|---|
EPA | 40 CFR Part 112 | Outlines requirements for oil spill prevention and response, including guidelines for containment booms. |
EPA | National Contingency Plan (NCP) | Provides a framework for responding to oil spills and includes guidelines for using containment booms. |
OSHA | 29 CFR 1910.120 | HAZWOPER standard outlining requirements for workers involved in hazardous spill response. |
OSHA | Personal Protective Equipment (PPE) | Requires appropriate PPE when deploying and handling spill containment booms. |
By using secondary containment berms, you’re not just protecting the environment—you’re also staying compliant with these critical regulations.
Key Takeaways
Secondary containment berms stop harmful spills from polluting nature. They work as barriers to catch leaks and protect soil and water.
Picking the right berm means checking material, size, and use. Make sure it holds 110% of the biggest container’s volume.
Checking and fixing berms often is very important. This finds damage early and keeps them working to stop spills.
Using these berms follows EPA and OSHA rules. It helps avoid big fines and keeps workplaces safe.
Strong berms save money over time. They lower cleanup costs and prevent work delays from spills.
What Are Secondary Containment Berms?
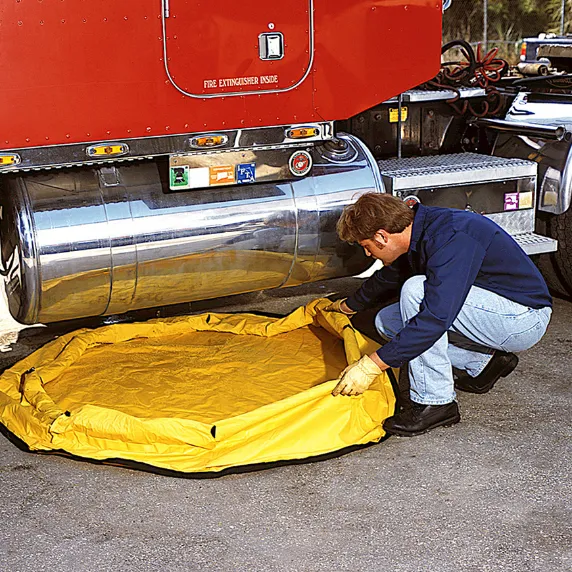
Definition and Purpose
Secondary containment berms are essential tools for managing spills in industrial and commercial settings. They act as barriers to capture and control leaks, spills, or discharges from primary storage containers. By doing so, they prevent hazardous substances from escaping into the environment. These berms protect soil and water from contamination, help you comply with environmental regulations, and reduce safety risks by limiting exposure to dangerous materials. Whether you’re storing oil, chemicals, or other liquids, secondary containment berms provide an extra layer of protection.
Types of Secondary Containment Berms
When it comes to choosing the right solution, you’ll find several types of spill containment berms designed for different needs.
Portable Berms
Portable spill containment berms are lightweight and easy to set up. You can quickly deploy them during emergencies or use them for temporary storage. They’re perfect for situations where flexibility and mobility are key.
Permanent Berms
Permanent spill containment berms are built to last. These are fixed structures designed for long-term use in facilities where spills are a constant concern. They’re ideal for areas like fuel storage sites or chemical plants.
Spill Containment Berms
General spill containment berms come in various designs to suit specific applications. Some are tailored for equipment washing stations, while others are used for fuel transfer or emergency spill response. No matter the type, they all serve the same purpose—keeping spills contained.
Materials Used in Secondary Containment Berms
The materials used in secondary containment berms determine their durability and effectiveness.
PVC and Polyurethane
PVC and polyurethane are popular choices for their flexibility and chemical resistance. These materials are often used in portable spill containment berms because they’re lightweight and easy to handle.
Metal and Composite Materials
Metal and composite materials are common in permanent spill containment berms. They offer superior strength and can withstand harsh conditions, making them ideal for long-term use.
By understanding the types of spill containment berms and the materials they’re made from, you can choose the right one for your needs.
How Do Secondary Containment Berms Work?
Design and Structure
Flexible Walls and Liners
The design of secondary containment berms focuses on flexibility and durability. Many portable spill containment berms feature flexible walls and liners made from materials like PVC or polyurethane. These materials are lightweight yet strong, making them easy to transport and set up. The flexible walls allow you to adjust the berm to fit different spaces or applications. Whether you’re dealing with a small spill or a larger containment need, these adaptable designs ensure you’re prepared for any situation.
Drainage and Overflow Features
Effective spill containment berms often include drainage and overflow features. These elements help manage excess liquid during a spill, preventing the berm from overflowing. For example, some designs incorporate valves or pumps to safely remove collected liquids. This ensures that the berm can handle spills without compromising its containment capacity. Additionally, these features make it easier for you to clean and maintain the berm after use.
Functionality in Spill Containment
Containing Hazardous Liquids
Secondary containment berms are designed to hold at least 110% of the largest container’s volume, ensuring they can handle even significant spills. This capacity is crucial for spill prevention, especially in industries dealing with hazardous liquids. Whether you’re storing oil, chemicals, or other substances, these berms act as a reliable barrier, keeping spills contained and preventing leaks from spreading.
Preventing Environmental Pollution
By containing hazardous liquids, spill containment berms play a vital role in protecting the environment. They prevent contaminants from seeping into the soil or water, reducing the risk of long-term damage. For instance, permanent spill containment berms made from durable materials like concrete are ideal for heavy-duty applications. They provide a robust solution for industries where environmental protection is a top priority.
Deployment and Maintenance
Quick Setup for Emergencies
In emergency situations, time is critical. Portable spill containment berms are designed for quick deployment, allowing you to respond to spills immediately. Their lightweight construction and user-friendly design make them easy to set up, even in challenging conditions. Whether you’re dealing with a spill during vehicle maintenance or at a decontamination station, these berms ensure you can act fast to minimize damage.
Regular Inspection and Care
To ensure your secondary containment berms remain effective, regular maintenance is essential. Periodic inspections help you identify and address issues like cracks or wear and tear. For permanent spill containment berms, resealing concrete and applying protective coatings can extend their lifespan. By taking these steps, you’ll keep your berms in top condition and ready for use whenever needed.
Uses of Secondary Containment Berms in Spill Control
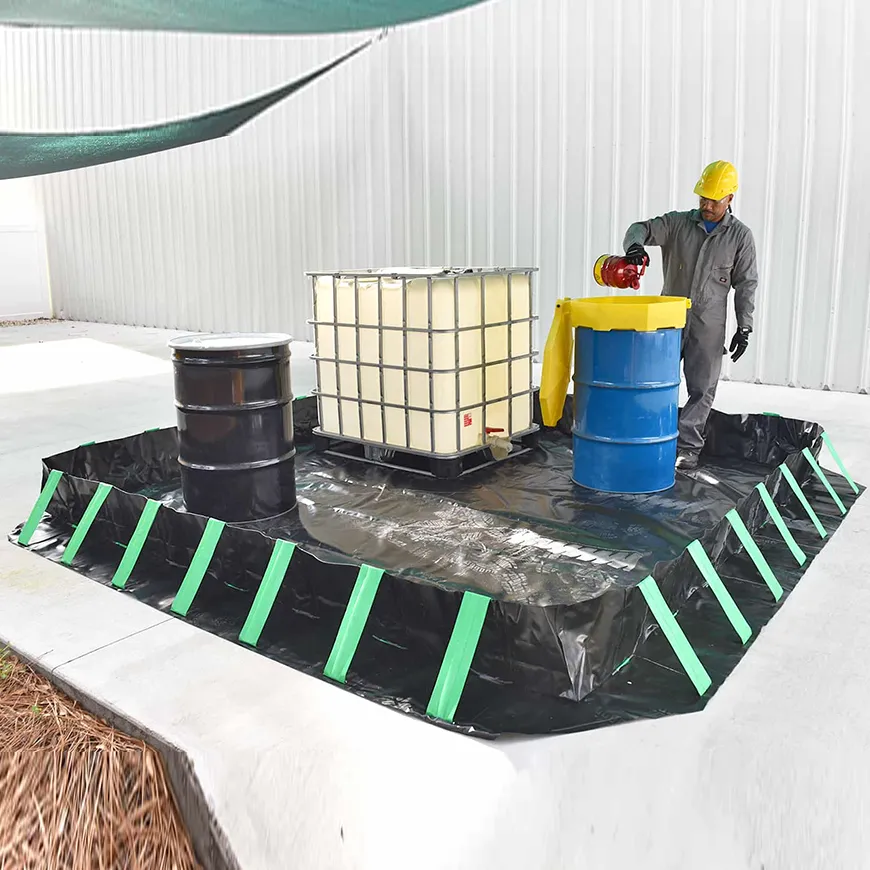
Industries That Use Secondary Containment Berms
Oil and Gas
If you work in the oil and gas industry, you know how critical spill control is. Secondary containment berms are a must-have for managing spills during operations. They’re used in several ways:
Portable Tanks: When transporting oil or fracking water, berms prevent spills during loading and unloading.
Bulk Storage: Large storage containers require berms to meet EPA regulations and avoid costly spills.
Drilling and Fracking Sites: Berms catch leaks and excess spillage from machinery, keeping the environment safe.
Maintenance Sections: Berms in these areas stop residual oils and chemicals from contaminating the ground.
Chemical Manufacturing
In chemical manufacturing, spills can be dangerous. Secondary containment berms protect workers and the environment by containing hazardous liquids. Whether it’s during chemical transfer or equipment maintenance, these berms ensure spills don’t spread. Permanent spill containment berms are especially useful for long-term storage of chemicals, offering a durable and reliable solution.
Transportation and Logistics
Spills during transportation can happen anytime. Portable spill containment berms are perfect for this industry because they’re easy to set up and move. They’re often used under vehicles during fueling or maintenance to catch leaks. This quick deployment helps you stay compliant with spill prevention regulations while keeping operations running smoothly.
Common Applications
Fuel Storage and Transfer
Fuel spills can cause serious damage. Secondary containment berms are commonly used during fuel storage and transfer to catch leaks and prevent contamination. Whether you’re working with portable tanks or permanent storage, these berms provide a reliable layer of protection.
Equipment Washing Stations
When washing equipment, runoff water often contains oils, grease, and other contaminants. Spill containment berms are placed around washing stations to collect this runoff, preventing it from polluting nearby soil or water.
Emergency Spill Response
In emergencies, you need a quick solution. Secondary containment berms act as catch basins to stop spills from spreading. They’re versatile, coming in different sizes to handle various containers and equipment. Whether it’s a decontamination station or a fueling operation, these berms help you respond effectively while staying compliant with EPA regulations.
Benefits of Using Secondary Containment Berms
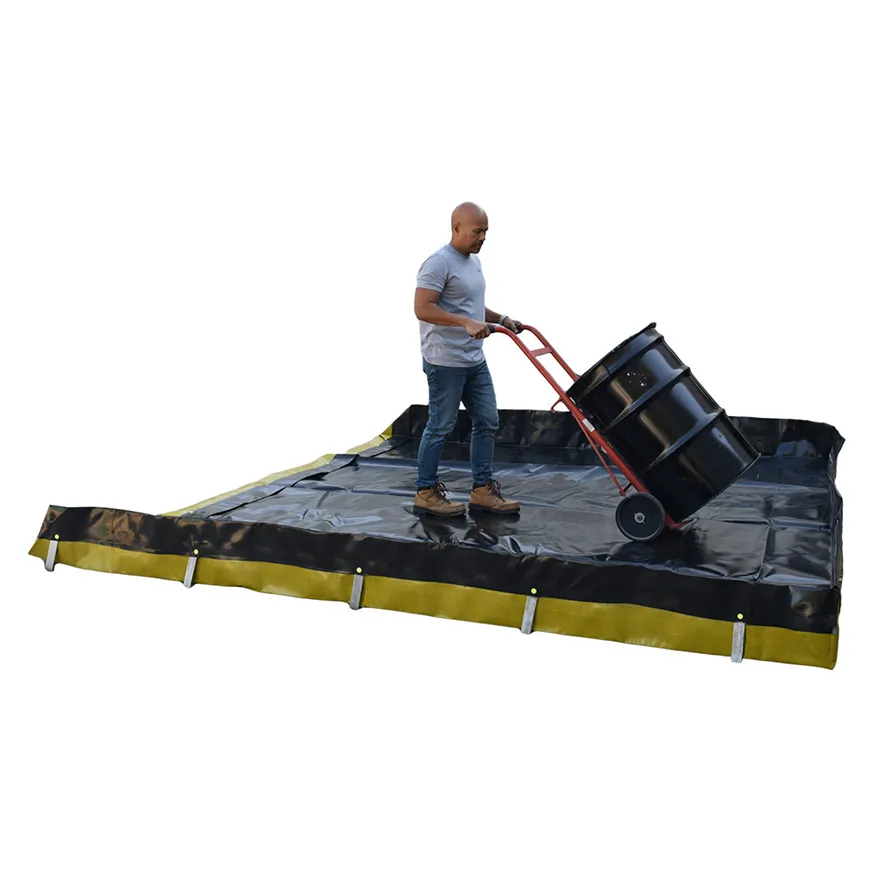
Environmental Protection
Preventing Soil and Water Contamination
Secondary containment berms are your first line of defense against environmental contamination. They capture spills, leaks, and discharges from primary storage containers, ensuring hazardous substances don’t escape into the environment. This protection is critical for safeguarding soil, groundwater, and surface water. For example, if a primary container fails, the berm prevents harmful chemicals from seeping into the ground or nearby water sources. By using these barriers, you also comply with environmental regulations, reducing risks to public health and safety.
Tip: Regularly inspect your berms to ensure they remain impermeable and effective in spill prevention.
Supporting Sustainability Goals
Using spill containment berms aligns with sustainability efforts. By preventing contamination, you reduce the need for extensive cleanup operations, which often involve heavy machinery and chemicals. This not only protects natural resources but also minimizes your carbon footprint. Additionally, these berms help you meet regulatory standards, which is a vital step toward achieving long-term environmental protection goals.
Key benefits of spill containment berms for sustainability:
They act as barriers to hazardous substances, protecting ecosystems.
They reduce environmental risks and protect public health.
They ensure compliance with spill prevention regulations.
Regulatory Compliance
Meeting EPA Standards
Staying compliant with EPA standards is easier with secondary containment berms. According to the Spill Prevention, Control, and Countermeasure (SPCC) rule, these berms must hold at least 110% of the largest container’s volume. They should also be made from durable, impermeable materials compatible with the stored substances.
Requirement | Description |
---|---|
Capacity | Must contain at least 110% of the volume of the largest primary container. |
Material | Constructed from durable materials compatible with stored substances. |
Impermeability | Must maintain impermeability to prevent leaks. |
Portable spill containment berms are especially useful for meeting these standards in industries like transportation and logistics.
Avoiding Fines and Penalties
Non-compliance with spill containment regulations can lead to hefty fines. For instance, facilities may face penalties exceeding $32,000 per day for violations. Even minor infractions, like failing to review an SPCC plan, can result in fines starting at $1,500. Beyond financial costs, non-compliance can lead to increased scrutiny, mandatory corrective actions, or even operational shutdowns. By investing in proper spill containment solutions, you avoid these risks and maintain smooth operations.
Cost-Effectiveness
Reducing Cleanup Costs
Spill containment berms save you money by limiting the extent of cleanup required after a spill. When a spill occurs, the berm contains it, preventing widespread contamination. This reduces labor costs, minimizes the need for expensive remediation efforts, and keeps your operations running smoothly. For example, a contained spill is easier and faster to clean up, which means less downtime for your team.
Minimizing Operational Disruptions
Spills can disrupt your workflow, but secondary containment berms help you avoid that. By acting as a reliable barrier, they prevent spills from spreading and causing damage to equipment or facilities. This protection ensures your operations stay on track, saving you time and money in the long run. Additionally, high-quality berms extend the life of your equipment by shielding it from corrosive substances.
Note: Investing in durable berms may seem costly upfront, but the long-term savings on cleanup, fines, and equipment maintenance make it worth every penny.
Tips for Choosing the Right Secondary Containment Berm

Material and Durability
When selecting a secondary containment berm, the material plays a huge role in its performance. You’ll want to choose a material that matches your specific needs. For example, PVC and polyurethane are lightweight and resistant to chemicals, making them great for portable berms. On the other hand, heavy-duty materials like polyethylene or urethane are better for high-traffic areas or long-term use. Durability is key if your berm will face frequent wear and tear.
Here’s a quick breakdown of factors to consider when choosing materials:
Factor | Description |
---|---|
Size and Capacity | Determine the maximum volume of liquid to contain and ensure the berm fits the available space. |
Material | Options include PVC, urethane, and polyethylene, each with unique strengths and weaknesses. |
Ease of Setup | Quick deployment is crucial in emergencies; some berms are designed for rapid setup. |
Portability | Lightweight berms are easier to transport and reposition, important for frequent movement. |
Durability | Essential for high-traffic areas; heavy-duty materials provide greater durability against wear. |
By considering these factors, you can ensure your berm is both effective and long-lasting.
Size and Capacity
Size matters when it comes to spill containment. You need a berm that can handle the largest container in your operation. Most regulations require the berm to hold at least 110% of the largest container’s volume. Measure your available space and ensure the berm fits without crowding the area. If you’re working in tight spaces, look for compact designs that still offer high capacity.
Portability and Ease of Use
If you need flexibility, portable berms are a smart choice. They’re lightweight, easy to move, and quick to set up. This makes them perfect for industries like transportation and logistics, where spills can happen in different locations. Portable berms also offer several benefits:
Environmental Protection: They prevent hazardous spills from contaminating soil and water.
Regulatory Compliance: They help you meet environmental standards and avoid fines.
Worker Safety: By containing spills, they reduce hazards and create safer conditions.
Cost Savings: They cut cleanup costs and lower the risk of legal fees.
When portability is a priority, these berms deliver convenience without compromising on performance.
Application-Specific Considerations
When choosing a secondary containment berm, you need to think about how it will perform in your specific application. Not all berms are created equal, and selecting the wrong one can lead to costly mistakes. Here are some key factors to keep in mind:
Material Compatibility: The material of the berm must match the type of liquid you’re containing. For example, certain chemicals like acids or solvents can damage some berm materials. If you’re dealing with harsh substances, look for berms made from chemically resistant materials like polyurethane or polyethylene.
Operating Conditions: Consider the environment where the berm will be used. Will it face extreme temperatures? If so, make sure the material can handle those conditions without cracking or degrading. Also, think about the pH level of the liquid. Highly acidic or alkaline substances require specialized materials to maintain the berm’s integrity.
Type of Contact: How will the liquid interact with the berm? If full immersion is likely, you’ll need a berm designed for that level of exposure. For lighter spills or occasional leaks, a less heavy-duty option might work just fine.
Consideration | Description |
---|---|
Material Compatibility | |
Structural Integrity | The berm should maintain impermeability to prevent leaks from escaping into the ground or surrounding areas. |
Regulatory Compliance | Systems must have the capacity to contain at least 110% of the volume of the largest primary container. |
Tip: Always check the manufacturer’s specifications to ensure the berm meets your needs. This can save you from unexpected failures during use.
By evaluating these factors, you can choose a berm that not only fits your application but also ensures safety and compliance. Remember, the right berm isn’t just a purchase—it’s an investment in protecting your operations and the environment.
Secondary containment berms are more than just barriers—they’re your first line of defense against spills. They stop hazardous substances from contaminating the environment, keep your operations compliant with EPA and OSHA standards, and improve workplace safety. By capturing leaks and spills, they also support long-term sustainability. Whether you need a portable or permanent solution, choosing the right berm ensures you’re prepared for any situation. Take a moment to assess your needs, from material to capacity, and invest in a berm that protects both your business and the planet.
Tip: Pair your berm with safety cans or containers for even greater spill control.
FAQ
What is the main purpose of a spill containment berm?
A secondary containment berm acts as a barrier to stop spills from spreading. It helps you contain hazardous liquids, protect the environment, and comply with regulations. Think of it as your safety net for spill control.
How do I choose the right material for my berm?
Pick a material based on the liquid you’re containing. For chemicals, go with chemically resistant options like polyurethane. For heavy-duty use, metal or composite materials work best. Always check compatibility with the substances you handle.
Are secondary containment berms reusable?
Yes, most berms are reusable! Portable ones, made from PVC or polyurethane, are especially easy to clean and reuse. Just inspect them regularly for damage to ensure they stay effective.
Do I need a berm for small spills?
Absolutely! Even small spills can cause big problems. A berm helps you contain leaks quickly, preventing contamination and saving you from costly cleanup or fines. It’s better to be safe than sorry.
Can I set up a berm by myself?
You sure can! Portable berms are designed for quick and easy setup. They’re lightweight and user-friendly, so you don’t need a team or special tools to get started.
Tip: Always follow the manufacturer’s instructions for the best results.
See Also
Evaluating UPQUARK Marine Absorbents for Effective Oil Cleanup
Understanding the Uses of Oil Absorbent Socks Effectively